I have a potential small reactor design that will alternate between high pH (10% by weigh NaOH, so 14+ pH) that is later taken to a slightly acidic side with HCl, resulting in a 6-10% salt (NaCl) solution. The reactor temperature will be ambient, so no high temp conditions. I've reviewed some literature on chloride pitting, and have mostly settled on C276 as my prime material of choice. I'm exploring different options, of course, but budgetary estimates for an Alloy 20 reactor were only about 10% less than a C276.
Before settling, I have ordered several corrosion tabs so I can place them in this reaction mass (acidic side), seeing what, if any, corrosion develops over the course of 6-8 weeks.
A couple of questions:
1. Given my reaction is ambient temperature, will heating the material for the corrosion tabs testing be beneficial for accelerating corrosion to see it in a short timeframe? Or should I keep the tab testing near temps the reactor will see?
2. Are the below charts generally correct? Any other materials or other corrosion mechanisms to watch out for?
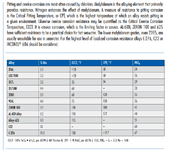
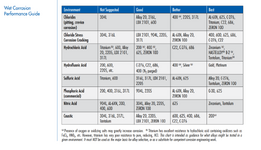
Before settling, I have ordered several corrosion tabs so I can place them in this reaction mass (acidic side), seeing what, if any, corrosion develops over the course of 6-8 weeks.
A couple of questions:
1. Given my reaction is ambient temperature, will heating the material for the corrosion tabs testing be beneficial for accelerating corrosion to see it in a short timeframe? Or should I keep the tab testing near temps the reactor will see?
2. Are the below charts generally correct? Any other materials or other corrosion mechanisms to watch out for?
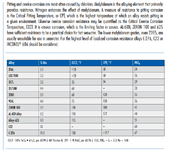
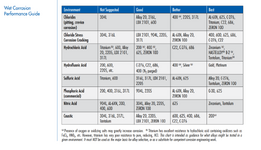