Hello,
We are weld repairing a pump case on IDs/bores and want to minimize case warpage. This is because warpage can cause other issues like more extra machining and additional work will be needed if case warps too much. Especially the case split lines need to be relatively flat (within 0.020") so we dont have to take too much from split lines when planning.
Case base material is Carbon steel and bores are welded with 309 weld overlay. Welding will be needed at location shown in below picture.
Things that I am planning to do to minimize warpage: Use TIG welding instead of stick, weld at different locations and give time to settle (while maintaining inter-pass temp) and minimize weld thickness. Any thing else that you can recommend?
That diameter needing welding is 14 inches.
We are weld repairing a pump case on IDs/bores and want to minimize case warpage. This is because warpage can cause other issues like more extra machining and additional work will be needed if case warps too much. Especially the case split lines need to be relatively flat (within 0.020") so we dont have to take too much from split lines when planning.
Case base material is Carbon steel and bores are welded with 309 weld overlay. Welding will be needed at location shown in below picture.
Things that I am planning to do to minimize warpage: Use TIG welding instead of stick, weld at different locations and give time to settle (while maintaining inter-pass temp) and minimize weld thickness. Any thing else that you can recommend?
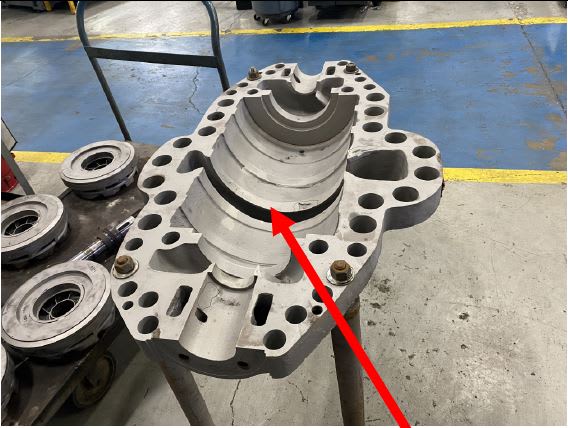
That diameter needing welding is 14 inches.