Hi, I'm an aerospace student working on a mechanical project. I'm redesigning an elevation mechanism and would love some guidance. The original transmission system, shown on the left, consists of a blue motor driving a green gearbox that generates the required torque to rotate a metal worm gear that's on the shaft. This shaft rotates two black supports that hold the rotating component.
However, the shaft running through the mechanism doesn't feel right. I want to redesign it to eliminate the need for a central shaft and have the full torque applied on one side while the other side moves freely. My redesigned concept is shown on the right, but it feels too simple, and I’m not sure if it's a good approach.
Any recommendation for a transmission system that would allow for a very precise rotation (+/- 0.5deg)? Does the redesign make sense?
However, the shaft running through the mechanism doesn't feel right. I want to redesign it to eliminate the need for a central shaft and have the full torque applied on one side while the other side moves freely. My redesigned concept is shown on the right, but it feels too simple, and I’m not sure if it's a good approach.
Any recommendation for a transmission system that would allow for a very precise rotation (+/- 0.5deg)? Does the redesign make sense?
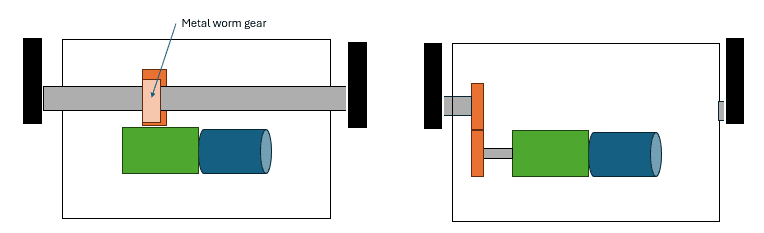