I am wanting to improve a planetary gearset in a cordless power tool. The current gearset creates a lot of noise and vibration. The motor spins at ~17,500 rpm, and the planetary gearset reduces it to ~4000 rpm at the output. The gear ratio is .228. The sun gear has 13 teeth, fixed ring gear has 44 teeth, and the three planet gears have 15 teeth each.
Currently the sun gear is on the motor shaft, the ring gear is fixed, and the planet carrier acts as the output. I am not tied to this configuration. I would like to keep a similar gear ratio but drastically reduce noise and vibration, while maintaining strong gears. The maximum motor torque (stall torque) is 0.23 N-m, so output torque is ~1 N-m. The current gears appear to be cast steel.
I have included pictures of the current gearset, including some pictures under a microscope. My initial research is pointing towards improving the manufacturing or the gear teeth and also applying a meshing phase difference to the planet gears. However, the world of gears seems to be very robust and intimidating. I am trying to read what I can but I quickly become lost. Can anyone help point me in the right direction to start my investigation? Also can anyone comment on the quality of the current gear teeth?
General assembly:
Planet Gear (magnification):
Ring Gear (magnification):
Currently the sun gear is on the motor shaft, the ring gear is fixed, and the planet carrier acts as the output. I am not tied to this configuration. I would like to keep a similar gear ratio but drastically reduce noise and vibration, while maintaining strong gears. The maximum motor torque (stall torque) is 0.23 N-m, so output torque is ~1 N-m. The current gears appear to be cast steel.
I have included pictures of the current gearset, including some pictures under a microscope. My initial research is pointing towards improving the manufacturing or the gear teeth and also applying a meshing phase difference to the planet gears. However, the world of gears seems to be very robust and intimidating. I am trying to read what I can but I quickly become lost. Can anyone help point me in the right direction to start my investigation? Also can anyone comment on the quality of the current gear teeth?
General assembly:
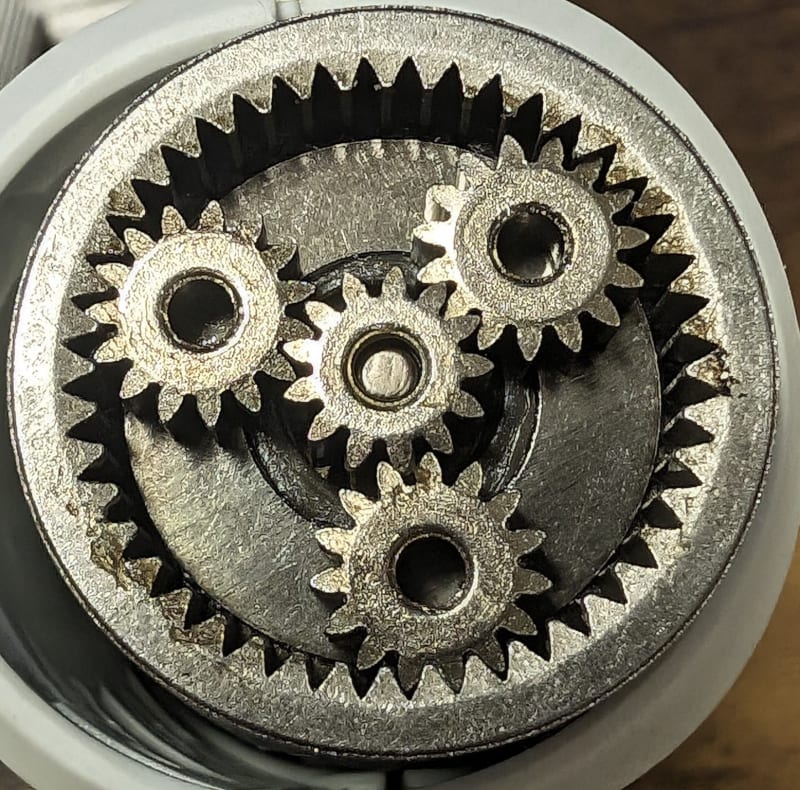
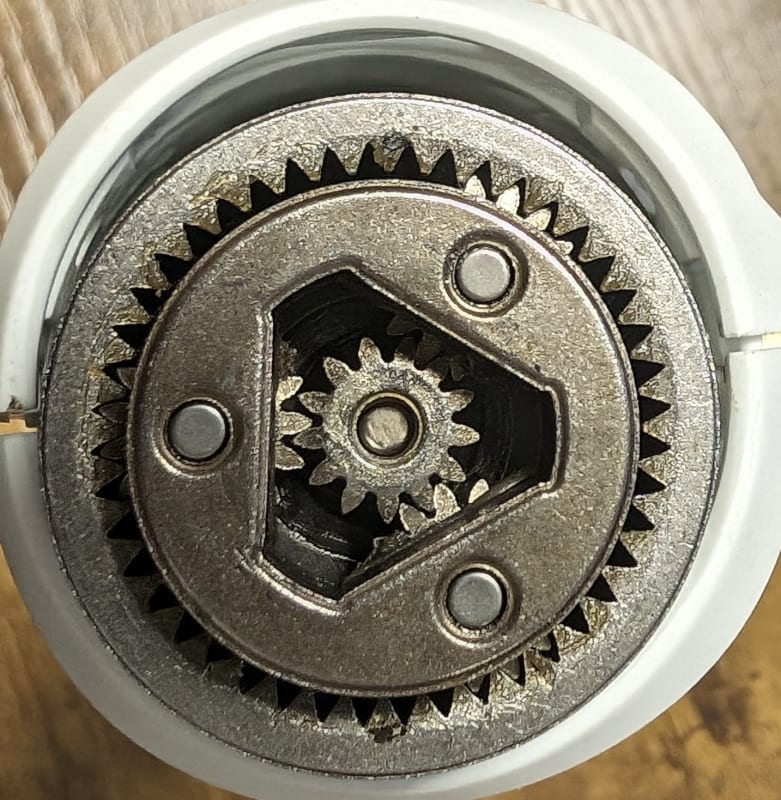

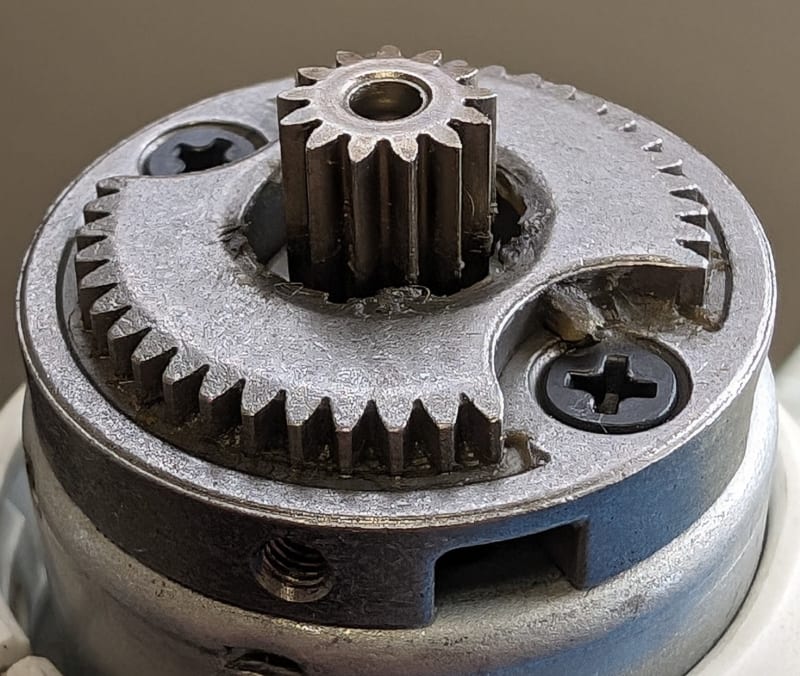
Planet Gear (magnification):
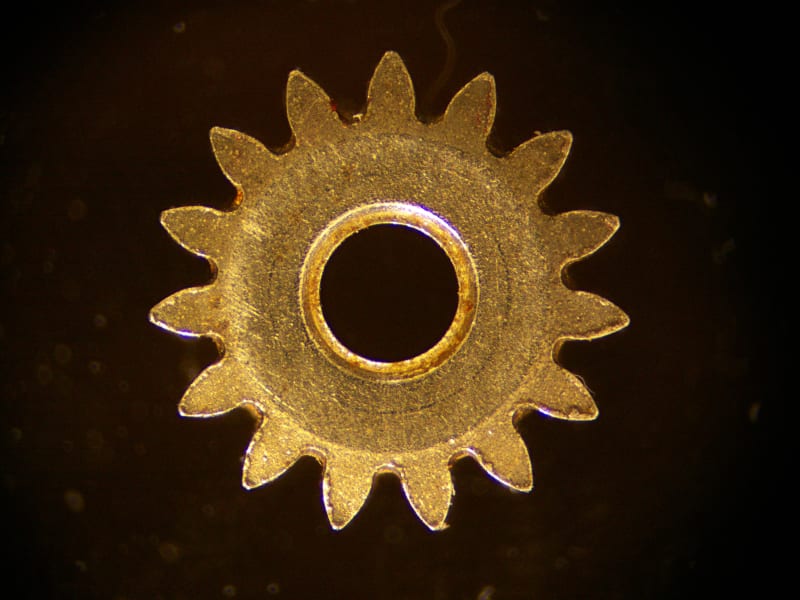
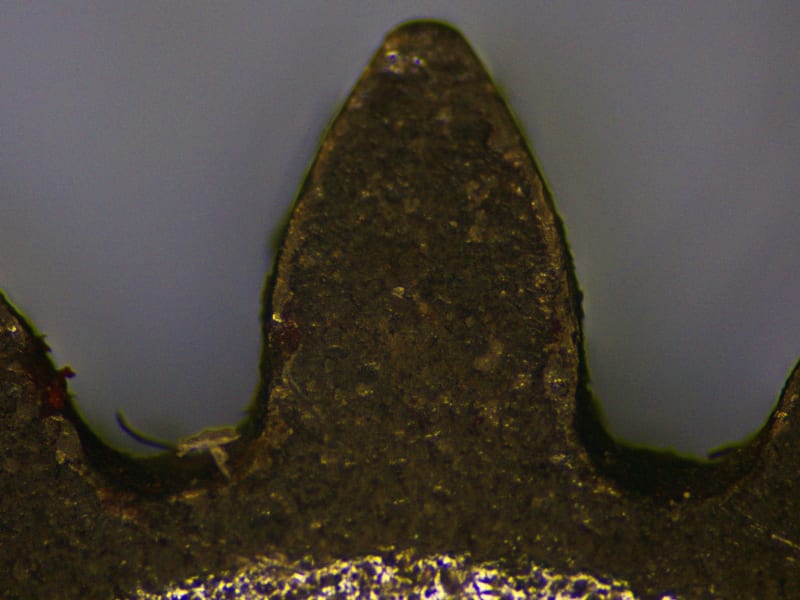
Ring Gear (magnification):
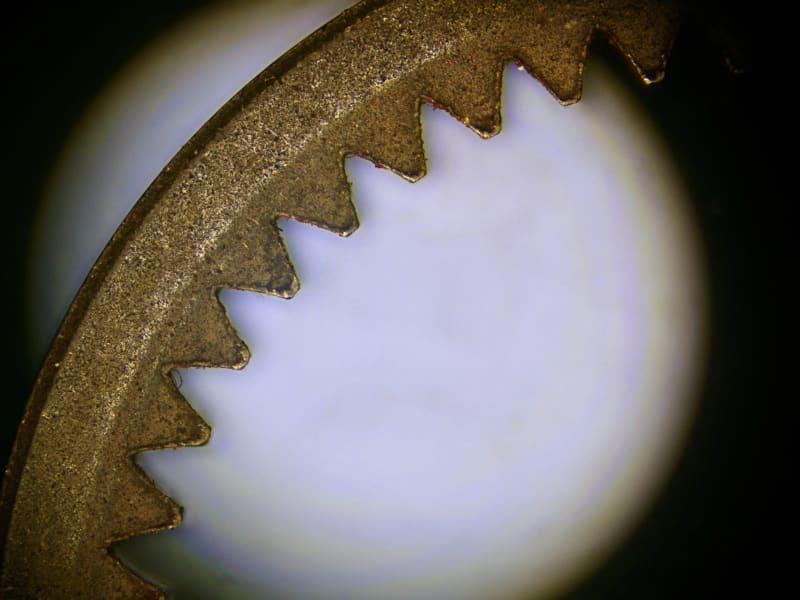
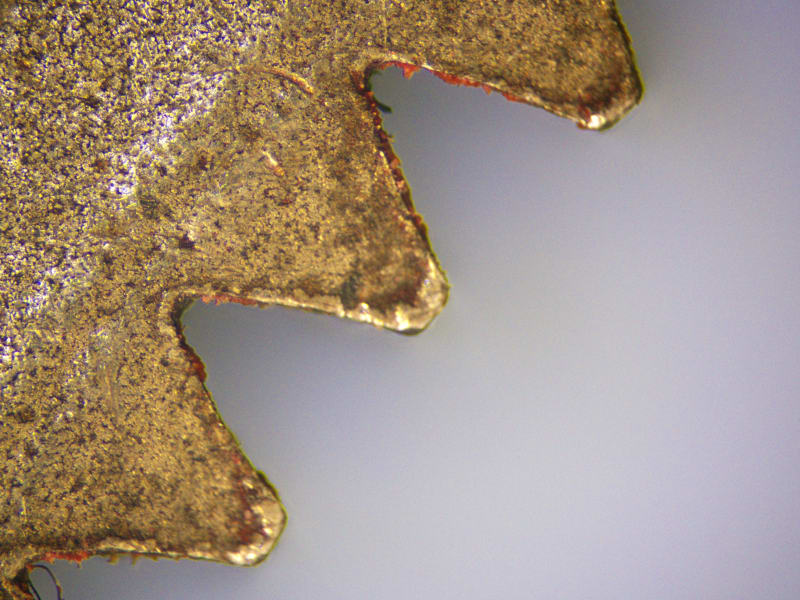