I am running into a problem checking the LTB on a W column. The column supports a carport with "hurricane wind" in Houston; it is being rotated in one direction by a "tilt beam" at the top. I have attached an illustration.
Basically the W column the designer wants to use seems to be failing in LTB (it's at about 150% capacity) because the unbraced length is so high. I am assuming K=2.1 for this scenario based on Table C-C2.2 of the AISC commentary (I have the 13th edition, black cover).
If we could reduce this unbraced length, it should check fine. Could we do this by simply welding warp-resisting plates to the hollows of the W beam, as shown in the illustration? Would this approach reduce the Lb and thus increase the critical moment capacity?
Basically the W column the designer wants to use seems to be failing in LTB (it's at about 150% capacity) because the unbraced length is so high. I am assuming K=2.1 for this scenario based on Table C-C2.2 of the AISC commentary (I have the 13th edition, black cover).
If we could reduce this unbraced length, it should check fine. Could we do this by simply welding warp-resisting plates to the hollows of the W beam, as shown in the illustration? Would this approach reduce the Lb and thus increase the critical moment capacity?
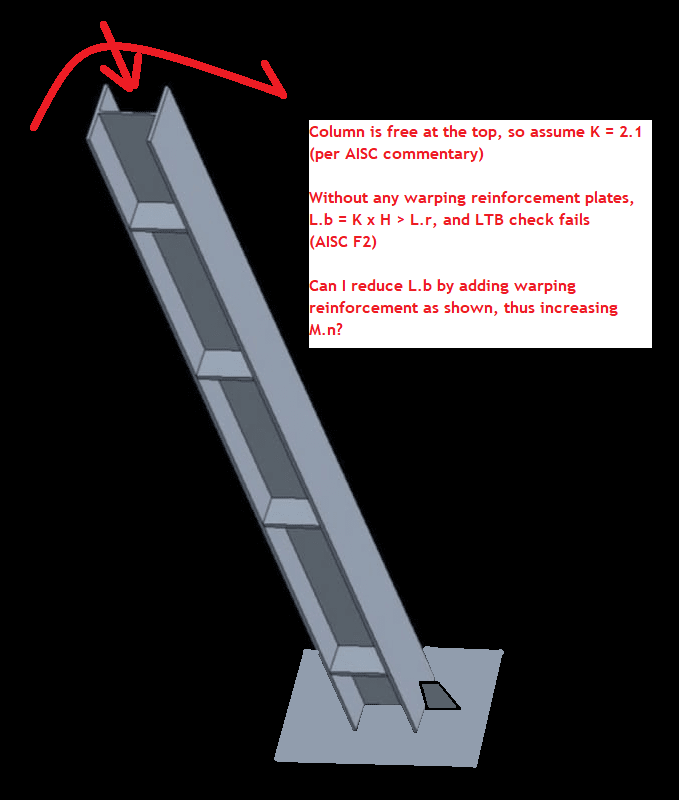