Siva Mareesan
Mechanical
Is that a rule in ASME Y14.5 2018 standard stating that the "Geometric tolerance should always be refinement of the size tolerance" which applies to all FORM, ORIENTATION , LOCATION , RUNOUT & PROFILE.
Here in the attachment, The Flatness Geometric tolerance is 0.25 which is less than size tolerance is 0.6. Will this applies to all other symbols too ?
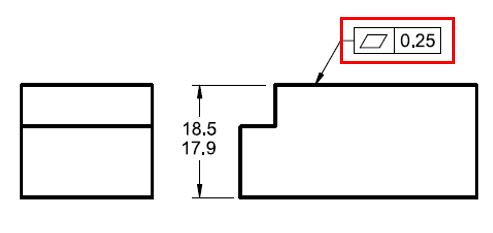
Here in the attachment, The Flatness Geometric tolerance is 0.25 which is less than size tolerance is 0.6. Will this applies to all other symbols too ?