Hello all,
I am trying to play with the hydraulic fluid simulator. I was trying the regenerative circuit to see the increase in cylinder speed during extraction. When I connect the rod end as attach in image1 I get slow speed but I connect as in image2 the cylinder advances real fast. What is the issue? Is there an issue with the simulator. Do both give equal results in real world
I am trying to play with the hydraulic fluid simulator. I was trying the regenerative circuit to see the increase in cylinder speed during extraction. When I connect the rod end as attach in image1 I get slow speed but I connect as in image2 the cylinder advances real fast. What is the issue? Is there an issue with the simulator. Do both give equal results in real world
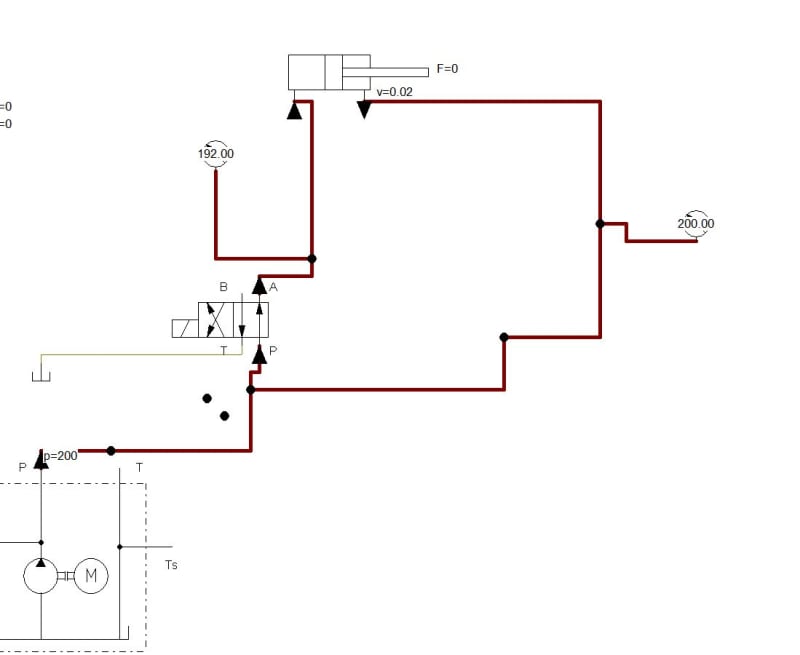
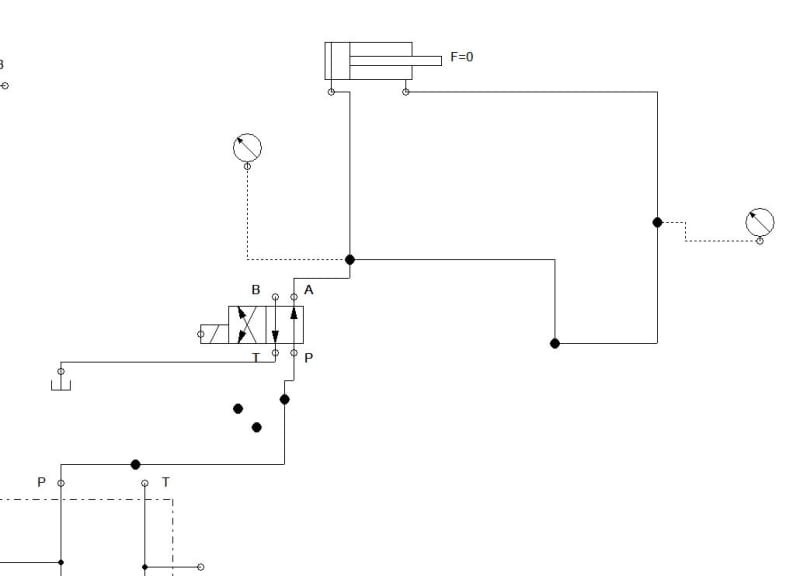