runcyclexcski
Bioengineer
Hi all,
I've been searching and posting all over the web about this issue. I apologize for the long question in advance.
I had a 304 tray welded at a welding shop specializing in stainless and laser-cutting. The part is a box about 2' x 1' x 1' with 1.2 mm-thick steel walls (~0.05") and a 1/4-thick flange for a gasket. The intended use is air humidification for indoor HVAC.
I have the certificates for the cold-rolled steel. The supplier is a large Belgian/French stainless company, the batch is from Dec 2023. For humification, the piece is supposed to be resistant to "regular" hardness tap water at mild temperatures (<100F), with occasional descale in tap water with 5% vinegar or 4% citric acid. Thus, I did not think at the time that 316 was necessary, and I've never had custom-made parts in 304 or 316 before; I always purchased standard off-the shelf parts.
The tray was welded directly from the raw SS sheets, without any additional processing. It arrived visually clean, with no fingerprints, and I gave it a rinse with water and "Fairy" detergent (similar to Dawn in the US). However, when I wiped it dry with lint-free scientific grade paper (kimwipes), I noticed a grey residue left on the paper. It did not seem a good idea to have this unknown "soot" in the air for breathing, so I spent the next few weeks trying to get rid of it.
A welding forum suggested that this was grease left over from machinning and welding. So I did a 5% vinegar rinse for 2 hrs, no effect. Then I did a 5% NaOH dip to degrease, followed by a 4% citric acid dip for 2 hrs at 170F (at the time I thought it was a passivation issue). This did not help either; in fact, it appeared to have made the residue worse.
It was then suggested to me at a metallurgy forum that I was dealing with smut left over from the steel manufacturing. This 1976 paper appears to describe what I am dealing with:
The paper above indicates that the only efficient methods to remove smut from 304 are concentrated HNO3, or chromic acid, or HF. The paper also mentioned electropolishing+HNO3. None of these are DIY-friendly methods, and I do not have access to a chemistry lab at the moment.
Should I give up on the piece and re-oder it in another material that is not as hard to clean and make corrosion-resistant? Or, I could try and outsource the desmutting/passivation. If I do, is there a standard protocol (USA or, preferentially, EU) that I should specifically request from the facility? There are shops within 1 hr who offer SS passivation, but HNO3 or electropolishing are not mentioned. I beleive they mostly do NaOH followed by citric acid -- and this has not helped, as I already tried.
Or, should I have the piece coated all over with PTFE or enamel? These options sound expensive, at least with a one-off piece like mine.
If I have to re-order this from scratch, what spec should I request -- HNO3 electropolishing, followed by an IPA smudge test of the finial product? Or use a differnet material, like a Ti Gr5?
Again, I apologize for the long question. This was driving me a bit insane for the last few weeks.
The picture shows the tray after the NaOH + citric acid treatment.
I've been searching and posting all over the web about this issue. I apologize for the long question in advance.
I had a 304 tray welded at a welding shop specializing in stainless and laser-cutting. The part is a box about 2' x 1' x 1' with 1.2 mm-thick steel walls (~0.05") and a 1/4-thick flange for a gasket. The intended use is air humidification for indoor HVAC.
I have the certificates for the cold-rolled steel. The supplier is a large Belgian/French stainless company, the batch is from Dec 2023. For humification, the piece is supposed to be resistant to "regular" hardness tap water at mild temperatures (<100F), with occasional descale in tap water with 5% vinegar or 4% citric acid. Thus, I did not think at the time that 316 was necessary, and I've never had custom-made parts in 304 or 316 before; I always purchased standard off-the shelf parts.
The tray was welded directly from the raw SS sheets, without any additional processing. It arrived visually clean, with no fingerprints, and I gave it a rinse with water and "Fairy" detergent (similar to Dawn in the US). However, when I wiped it dry with lint-free scientific grade paper (kimwipes), I noticed a grey residue left on the paper. It did not seem a good idea to have this unknown "soot" in the air for breathing, so I spent the next few weeks trying to get rid of it.
A welding forum suggested that this was grease left over from machinning and welding. So I did a 5% vinegar rinse for 2 hrs, no effect. Then I did a 5% NaOH dip to degrease, followed by a 4% citric acid dip for 2 hrs at 170F (at the time I thought it was a passivation issue). This did not help either; in fact, it appeared to have made the residue worse.
It was then suggested to me at a metallurgy forum that I was dealing with smut left over from the steel manufacturing. This 1976 paper appears to describe what I am dealing with:
The paper above indicates that the only efficient methods to remove smut from 304 are concentrated HNO3, or chromic acid, or HF. The paper also mentioned electropolishing+HNO3. None of these are DIY-friendly methods, and I do not have access to a chemistry lab at the moment.
Should I give up on the piece and re-oder it in another material that is not as hard to clean and make corrosion-resistant? Or, I could try and outsource the desmutting/passivation. If I do, is there a standard protocol (USA or, preferentially, EU) that I should specifically request from the facility? There are shops within 1 hr who offer SS passivation, but HNO3 or electropolishing are not mentioned. I beleive they mostly do NaOH followed by citric acid -- and this has not helped, as I already tried.
Or, should I have the piece coated all over with PTFE or enamel? These options sound expensive, at least with a one-off piece like mine.
If I have to re-order this from scratch, what spec should I request -- HNO3 electropolishing, followed by an IPA smudge test of the finial product? Or use a differnet material, like a Ti Gr5?
Again, I apologize for the long question. This was driving me a bit insane for the last few weeks.
The picture shows the tray after the NaOH + citric acid treatment.
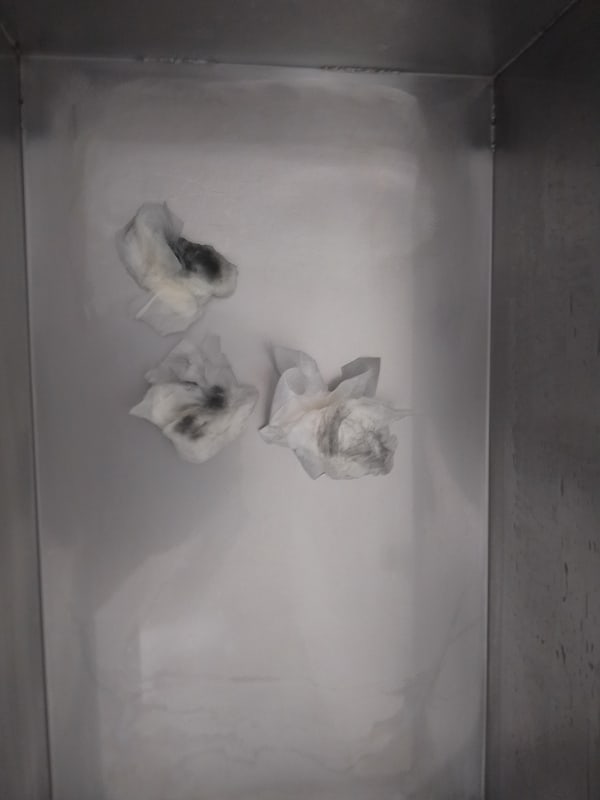