Good morning.
I need to create a device (or valve) to reduce de pressure in the exhaust pipe of a compressor, from pressures between 1,1 and 10 bara to atmospheric pressure, so I need to create a range of drop pressure in some device that I could ajust the area.
The device is simple, with 2 discs, one fixed in the pipe and a rotating one closing or opening radial oblongs (sketch attached).
My issue here is how to determine the required area for the pressure drop, I'm studying some materials on the internet, but I'm still cant get the formula done to put in a sheet to evaluate all the required areas.
I have all the properties of the air in the required working conditions, I just didnt realize yet how the make the equation to get the required area for the pressure drop.
I've tried to use this material from NASA but I've get confused and my formulas didnt work.
Below is one case:
D1 = 350 mm (pipe diameter before valve);
m1 = 7,8 kg/s (massic flow);
P1 = 5,8 bara (pressure before valve);
T1 = 325,36 °C (air temperature);
ρ1 = 3,38 kg/m³ (density before valve);
V1 = 24,63 m/s (air speed before valve)
γ1 = 1,375 (gamma factor Cp/Cv for T1)
Ao - ? (Orifice plate required area);
D2 = 600 mm (pipe diameter after valve);
m2 = m1;
P2 = 1 bara (atmospheric);
T2 = T1;
ρ2 = 0,58 kg/m³ (density after valve);
V2 = 47,76 m/s (air speed after valve);
Could someone give me a help with this equation ?
Thanks in advanced.
Barata
I need to create a device (or valve) to reduce de pressure in the exhaust pipe of a compressor, from pressures between 1,1 and 10 bara to atmospheric pressure, so I need to create a range of drop pressure in some device that I could ajust the area.
The device is simple, with 2 discs, one fixed in the pipe and a rotating one closing or opening radial oblongs (sketch attached).
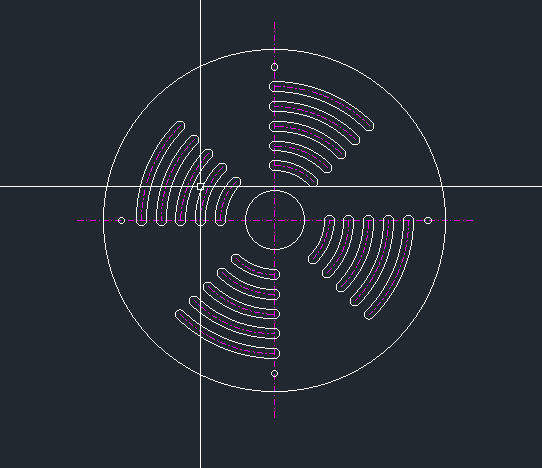
My issue here is how to determine the required area for the pressure drop, I'm studying some materials on the internet, but I'm still cant get the formula done to put in a sheet to evaluate all the required areas.
I have all the properties of the air in the required working conditions, I just didnt realize yet how the make the equation to get the required area for the pressure drop.
I've tried to use this material from NASA but I've get confused and my formulas didnt work.
Below is one case:
D1 = 350 mm (pipe diameter before valve);
m1 = 7,8 kg/s (massic flow);
P1 = 5,8 bara (pressure before valve);
T1 = 325,36 °C (air temperature);
ρ1 = 3,38 kg/m³ (density before valve);
V1 = 24,63 m/s (air speed before valve)
γ1 = 1,375 (gamma factor Cp/Cv for T1)
Ao - ? (Orifice plate required area);
D2 = 600 mm (pipe diameter after valve);
m2 = m1;
P2 = 1 bara (atmospheric);
T2 = T1;
ρ2 = 0,58 kg/m³ (density after valve);
V2 = 47,76 m/s (air speed after valve);
Could someone give me a help with this equation ?
Thanks in advanced.
Barata