BndStructural
Structural
- Jan 16, 2024
- 14
Hello,
I have received a project of a high-end custom home on a sloped lot. The slope is steep downwards from the right of way. The driveway will be used as a bridge to the garage and main level of the home. Finished space will exist under the garage that will be used for storage. I have worked on many elevated garages built directly on the concrete foundation walls, but never another story above or on wood framed walls. The home designer has asked me to come up with the design and has provided no input. I typically would lean towards steel wide flange beams and a one-way slab resting on the stem walls with a sloped bearing pad. Do I still use wide flange beams and a one-way slab, but instead bear on a wood wall? Do I to tell the designer that wood walls are not a good idea? I see wood floor framing used all the time. but I myself have stayed away from it. To add, the owner intends to install a car lift in one corner to be used to store one car in the air on the lift and another underneath that car. What design concerns should I consider here?
I have received a project of a high-end custom home on a sloped lot. The slope is steep downwards from the right of way. The driveway will be used as a bridge to the garage and main level of the home. Finished space will exist under the garage that will be used for storage. I have worked on many elevated garages built directly on the concrete foundation walls, but never another story above or on wood framed walls. The home designer has asked me to come up with the design and has provided no input. I typically would lean towards steel wide flange beams and a one-way slab resting on the stem walls with a sloped bearing pad. Do I still use wide flange beams and a one-way slab, but instead bear on a wood wall? Do I to tell the designer that wood walls are not a good idea? I see wood floor framing used all the time. but I myself have stayed away from it. To add, the owner intends to install a car lift in one corner to be used to store one car in the air on the lift and another underneath that car. What design concerns should I consider here?
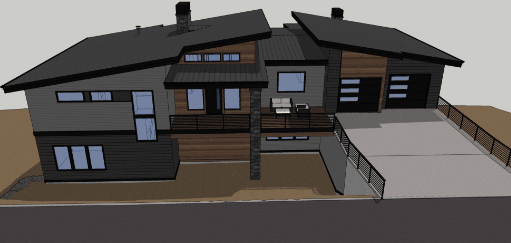
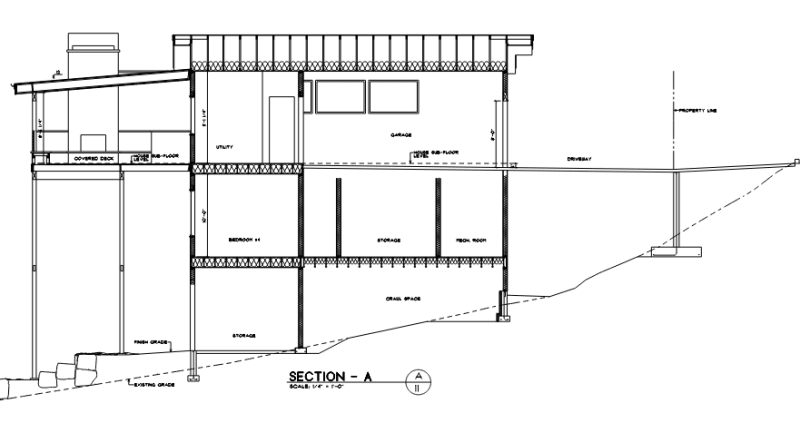