Hello, I am trying to experiment with nonlinear adaptive meshing and I made a quick test 2D plane stress model.
In the model, a rigid body 'tool' uses a prescribed displacement to contact a billet as a flexible body. The flexible body is fixed in the x-axis on it's sides and x/y on its base. The material is a copper with a bi-linear isotropic hardening plasticity model (a default ansys material). It's a simple model and it doesn't really represent any real process, but when I was looking at the results, I was wondering how do you interpret residual stress after gross-plasticity? Obviously yield is increased after the load is removed, but how is residual stress in this model is still way over yield? Initial yield is 280 MPa. Is this possibly because the data file does not contain a data point beyond 0.0127 strain? Maybe I am misunderstanding something about residual stress?
Thanks for your help!
In the model, a rigid body 'tool' uses a prescribed displacement to contact a billet as a flexible body. The flexible body is fixed in the x-axis on it's sides and x/y on its base. The material is a copper with a bi-linear isotropic hardening plasticity model (a default ansys material). It's a simple model and it doesn't really represent any real process, but when I was looking at the results, I was wondering how do you interpret residual stress after gross-plasticity? Obviously yield is increased after the load is removed, but how is residual stress in this model is still way over yield? Initial yield is 280 MPa. Is this possibly because the data file does not contain a data point beyond 0.0127 strain? Maybe I am misunderstanding something about residual stress?
Thanks for your help!
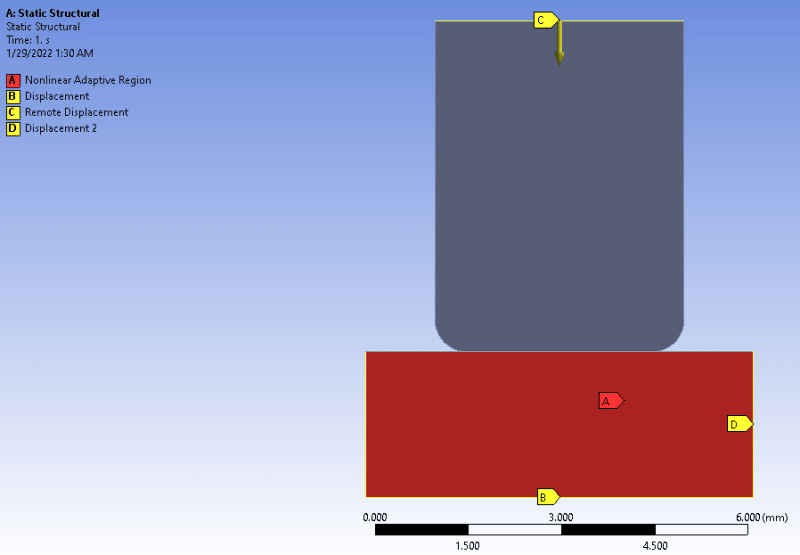
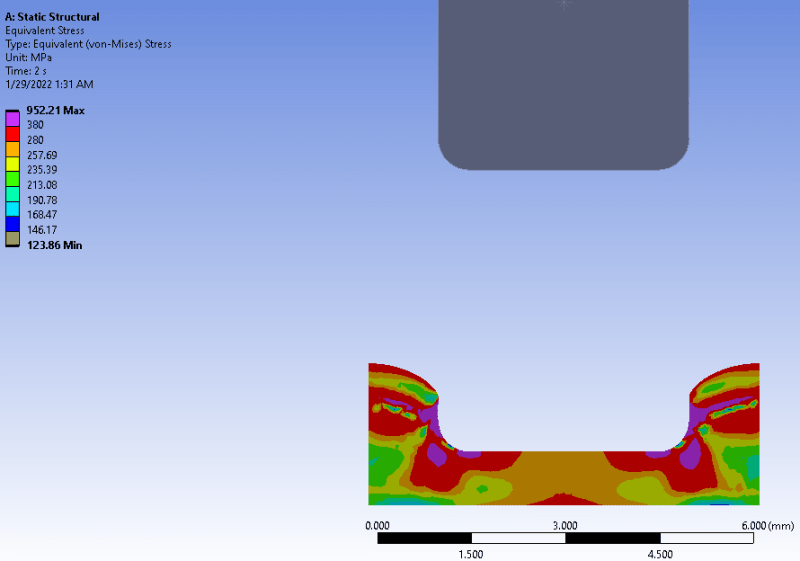
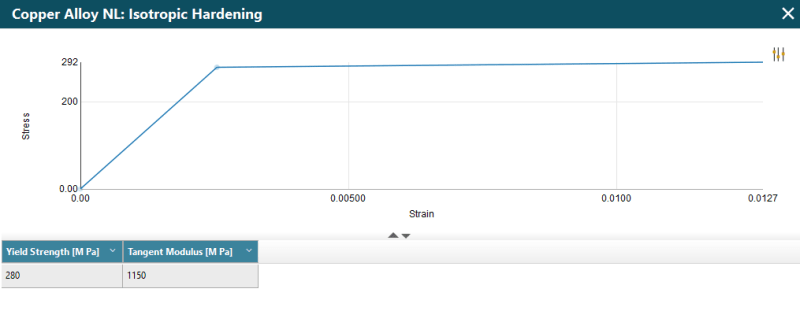