Hi all! Hope everyone had a great Christmas and is ready to get back to the grind!
I have a situation in which I would like to get some input from you forumers. I have an HSS beam that must tie into a girder and then follow with an overhang. Due to height restrictions I cannot afford to stack the beam over top of the girder. Currently I have an HSS beam that frames into an HSS girder for ease of connection (welded moment connections). I would fundamentally like for this system to behave similar to a beam running over top of a girder which relies on the girder only to pick up vertical load and zero torsion. I want the end reaction of the HSS girder to the column to only be a vertical load. With my beam framing into the girder & forming a moment connection for continuity, the beam will induce rotation in the girder that it attaches to. This rotation induces torsion and leads into the issue that I am currently grappling with:
Now that I have induced torsion in my girder, unless the beam would warp to infinity, the ends of my beams will have torsional loads. With my choosing an HSS girder, warping is restrained and thus I have a large torsional force at my connection point of my HSS girder back to the web of my existing column. I ultimately do not want to dump this torsion into the column which would be a moment about the strong axis of the existing of the column, rather I would like the connection to be torsionally released. Realistically however, in order for this to occur, if I create a cap plate with shear tab connection for the HSS girder to column connection, the shear tab would have to rotate/warp in order to not transfer this torsion load into the existing columns. This fundamentally does not seem like something I would like to do. Is this typically a scenario that many people wave their hands over & ignore, simply put, if you did not design your connection to transfer torsion then their will be no transfer of torsion? In my situation it would seem that I cannot ignore the torsion that would be transferred from my HSS girder to shear tab connection.
Ultimately I may have use an Wide Flange Shape for the girder as to promote warping and reduce the torsional load at the connection to be minimal & much less than with an HSS Girder.
Am I viewing the load path and subsequent design assumptions here similarly to how any of your forumers would? Your input is greatly appreciated. Also, I have attached a rudimentary sketch for clarification.
Thank you!
I have a situation in which I would like to get some input from you forumers. I have an HSS beam that must tie into a girder and then follow with an overhang. Due to height restrictions I cannot afford to stack the beam over top of the girder. Currently I have an HSS beam that frames into an HSS girder for ease of connection (welded moment connections). I would fundamentally like for this system to behave similar to a beam running over top of a girder which relies on the girder only to pick up vertical load and zero torsion. I want the end reaction of the HSS girder to the column to only be a vertical load. With my beam framing into the girder & forming a moment connection for continuity, the beam will induce rotation in the girder that it attaches to. This rotation induces torsion and leads into the issue that I am currently grappling with:
Now that I have induced torsion in my girder, unless the beam would warp to infinity, the ends of my beams will have torsional loads. With my choosing an HSS girder, warping is restrained and thus I have a large torsional force at my connection point of my HSS girder back to the web of my existing column. I ultimately do not want to dump this torsion into the column which would be a moment about the strong axis of the existing of the column, rather I would like the connection to be torsionally released. Realistically however, in order for this to occur, if I create a cap plate with shear tab connection for the HSS girder to column connection, the shear tab would have to rotate/warp in order to not transfer this torsion load into the existing columns. This fundamentally does not seem like something I would like to do. Is this typically a scenario that many people wave their hands over & ignore, simply put, if you did not design your connection to transfer torsion then their will be no transfer of torsion? In my situation it would seem that I cannot ignore the torsion that would be transferred from my HSS girder to shear tab connection.
Ultimately I may have use an Wide Flange Shape for the girder as to promote warping and reduce the torsional load at the connection to be minimal & much less than with an HSS Girder.
Am I viewing the load path and subsequent design assumptions here similarly to how any of your forumers would? Your input is greatly appreciated. Also, I have attached a rudimentary sketch for clarification.
Thank you!
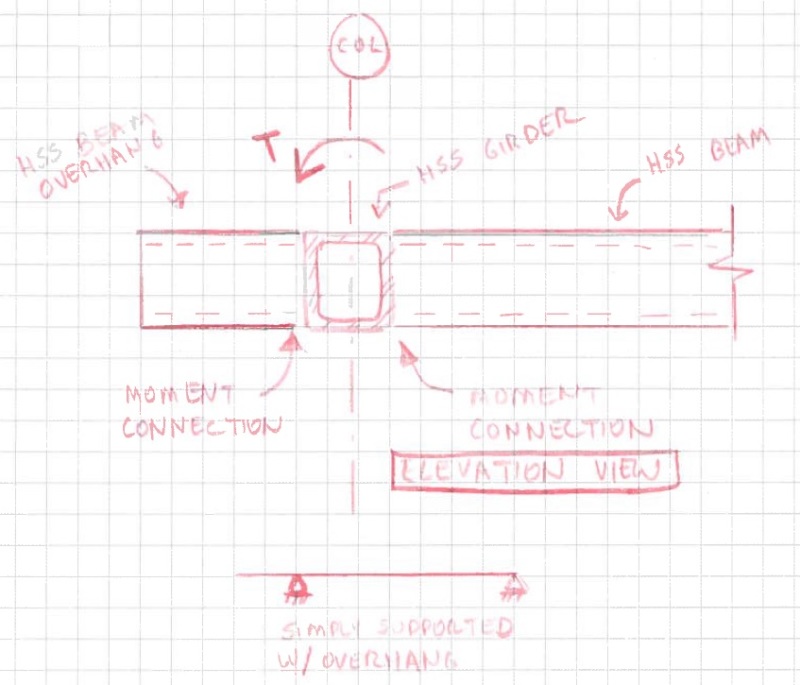