I am trying to make a sort of reverse Whitworth Quick Return Mechanism in which I am converting this oscillating arm movement into a rotational movement rather than the other way around, it looks like the mechanism should work in reverse however in practice the oscillating arm just pushes the rotating wheel back and forth rather than doing a full rotation as seen in the gif. Any ideas on how I can make this work?
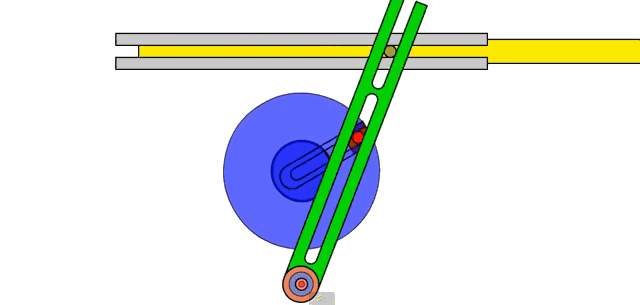