I have been trying to create a body of revolution in FEMAP but I am having issues with small cells when it is near the axis of revolution. This is shown in the attached figure where the top rows of element are somehow merged. Does anyone have a good solution for this or know why it is happening?
As further information, I know the elements wouldn't be great for structural modelling, but I am intending to use the mesh for aerodynamics.
Thanks
Ian
As further information, I know the elements wouldn't be great for structural modelling, but I am intending to use the mesh for aerodynamics.
Thanks
Ian
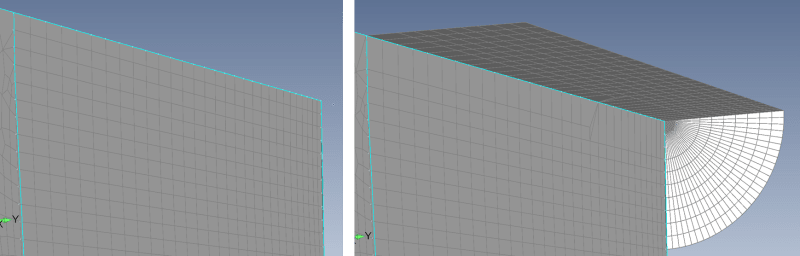