Richard888
Automotive
Hi guys I'm new here and in need of your professional advice.
I have a burnt Karcher HD 6/15C pressure washer. The motor was a 230Vac single phase 50Hz 3.1kw we connect it to 230Vac 60Hz and the windings get burnt.
Now I'd like to rewind it and I've been searching the net on how to convert it to same voltage but at 60Hz.
Do I need to increase the turns by 60/50 and reduce the wire size by 50/60 in circular mils for me to convert it from 50Hz to 60Hz motor? and also do I need to change the capacitor value?
Thanks
Starting Coil
Running Coil
I have a burnt Karcher HD 6/15C pressure washer. The motor was a 230Vac single phase 50Hz 3.1kw we connect it to 230Vac 60Hz and the windings get burnt.
Now I'd like to rewind it and I've been searching the net on how to convert it to same voltage but at 60Hz.
Do I need to increase the turns by 60/50 and reduce the wire size by 50/60 in circular mils for me to convert it from 50Hz to 60Hz motor? and also do I need to change the capacitor value?
Thanks
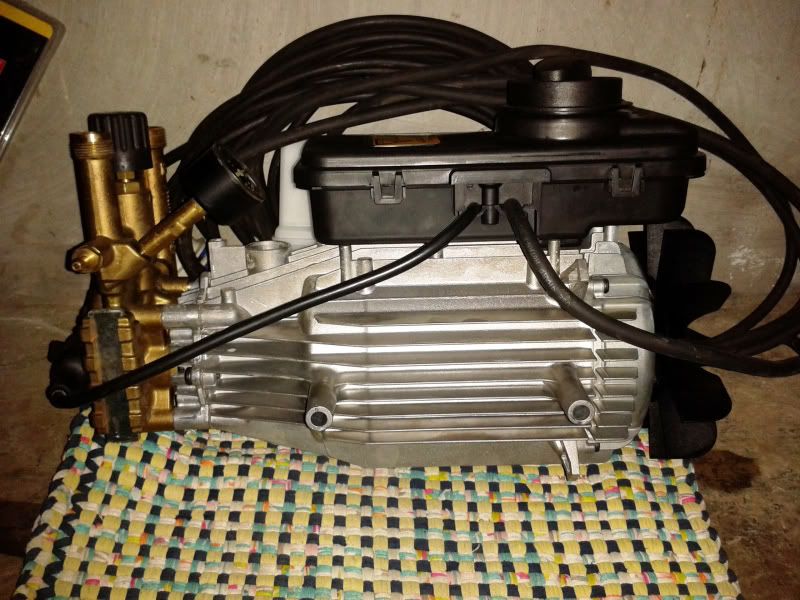
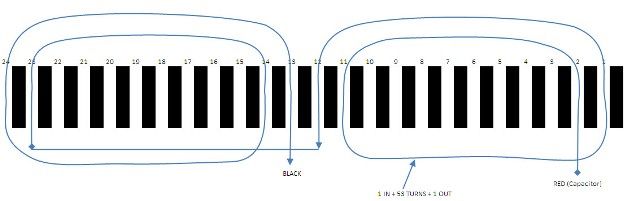
Starting Coil
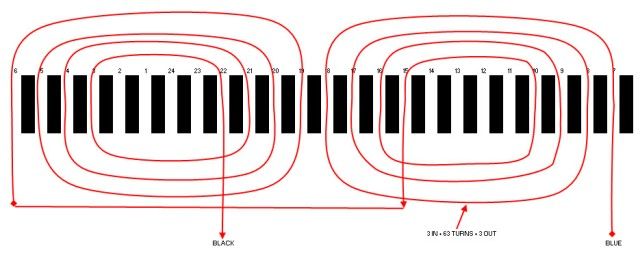
Running Coil