Hi guys,
I'm currently working on a project where the client has requested the removal of a steel column, and I am tasked with designing a rigid connection to replace it. The project involves connecting two steel beams at point 2, with a span of 8.2 feet from point 1 to point 2 and a sloped section of 10.8 feet from point 2 to point 3.
I have designed the steel beams as continuous beams with satisfactory sizing. At the connection point 2, I have utilized two plates bolted together with four bolts and welded to the beams, which also appears to be satisfactory. However, I would greatly appreciate your input to ensure that I am not overlooking any critical factors in the design.
Thank you for your assistance.
I'm currently working on a project where the client has requested the removal of a steel column, and I am tasked with designing a rigid connection to replace it. The project involves connecting two steel beams at point 2, with a span of 8.2 feet from point 1 to point 2 and a sloped section of 10.8 feet from point 2 to point 3.
I have designed the steel beams as continuous beams with satisfactory sizing. At the connection point 2, I have utilized two plates bolted together with four bolts and welded to the beams, which also appears to be satisfactory. However, I would greatly appreciate your input to ensure that I am not overlooking any critical factors in the design.
Thank you for your assistance.
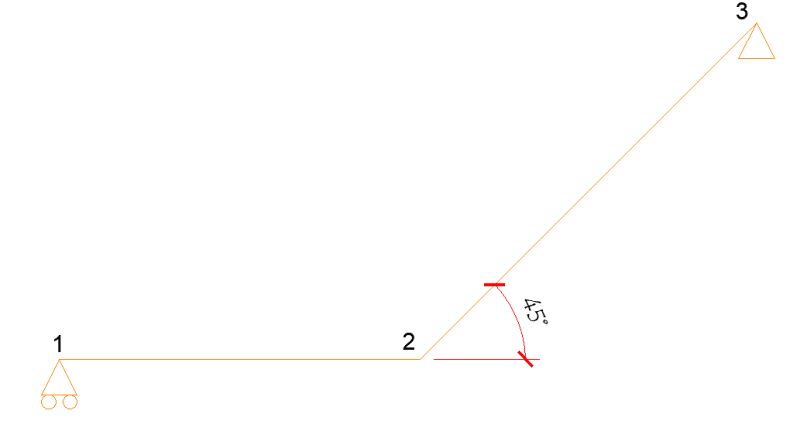