I have a question for you all about rim joists and shear transfer. Typically, I design the wall sheathing to break at the top of the top plates and then attach LTP4 clips at the joint to transfer the load through the joint. My client, however, wants to place the joint mid-height of the rim joist. I've said this was okay and have detailed it as a continuous solid LVL rim joist. They have now started using rim joists as trusses, instead of the LVL. The rim joists have a horizontal web, as shown in the attached image, which is where the sheathing breaks. The truss engineer is wanting to know if the truss needs to be designed for the shear load or not, as if it does need to, it fails. My client is freaking out over this so i'm trying to dig deeper into this. The shear load only goes through that horizontal blocking, and then back out of it, less than 1/2" away, so the entire truss wouldn't feel the shear transfer, is that correct?
I'd love to hear input on whether or not the rim truss needs to be designed for the full shear load here.
I'd love to hear input on whether or not the rim truss needs to be designed for the full shear load here.
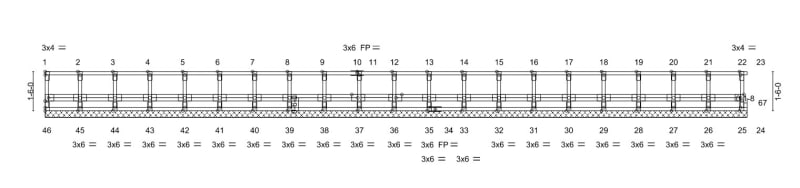
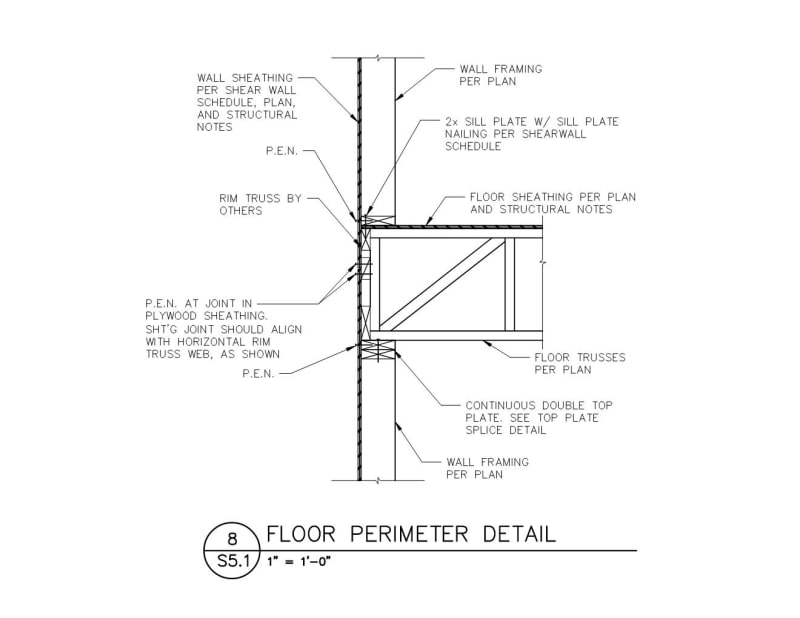