I am using RISA for the first time to design an small industrial platform that will be used for man access to mechanical equipment (Note mechanical equipment is independent of the platform and does not impart a load on the platform). The reason I am doing this in RISA this time is the platform beams are not nice and concentric with the columns of end and intermediate frames. I also do not have much opportunity with the equipment below to add any braces in one of the directions.
The platform dimensions are noted in the attached sketch along with RISA results (3 ft wide, 18 ft long, 7.5 ft high platform). I am not seeing very large loads or deflections in any of the members or joints which I find promising but I am cautious that I might be missing something. The design constraints and assumptions are as follows and my questions are below.
Constraints:
- Platform width is driven by access between piping so no opportunity to make it wider.
- End and Intermediate frames have less restrictions space wise and are wider.
- I only have the ability to add bracing in one direction as shown.
Assumptions:
- 100 PSF LL
- 10 PSF (Bar Grating) + Self Weight & Handrail DL
- Lateral Loads of ~2% of factored vertical loads at each node in both X & Z direction. (This is based on ASCE 7 1.4.3, I believe it is fairly conservative given ASCE calls for 1% of Dead Load)
Questions:
- With the relatively small loads and deflections is it reasonable to have bracing in only one direction and utilize the stiffness of the columns and base plate connection to develop the loads in the X direction? (I am hesitant to assume the base plate connection is in reality "fully fixed")
- Is there anything that sticks out in the model view that doesn't look right?
- Any general tips using RISA for design.
I appreciate all the help and input!
Thanks
The platform dimensions are noted in the attached sketch along with RISA results (3 ft wide, 18 ft long, 7.5 ft high platform). I am not seeing very large loads or deflections in any of the members or joints which I find promising but I am cautious that I might be missing something. The design constraints and assumptions are as follows and my questions are below.
Constraints:
- Platform width is driven by access between piping so no opportunity to make it wider.
- End and Intermediate frames have less restrictions space wise and are wider.
- I only have the ability to add bracing in one direction as shown.
Assumptions:
- 100 PSF LL
- 10 PSF (Bar Grating) + Self Weight & Handrail DL
- Lateral Loads of ~2% of factored vertical loads at each node in both X & Z direction. (This is based on ASCE 7 1.4.3, I believe it is fairly conservative given ASCE calls for 1% of Dead Load)
Questions:
- With the relatively small loads and deflections is it reasonable to have bracing in only one direction and utilize the stiffness of the columns and base plate connection to develop the loads in the X direction? (I am hesitant to assume the base plate connection is in reality "fully fixed")
- Is there anything that sticks out in the model view that doesn't look right?
- Any general tips using RISA for design.
I appreciate all the help and input!
Thanks

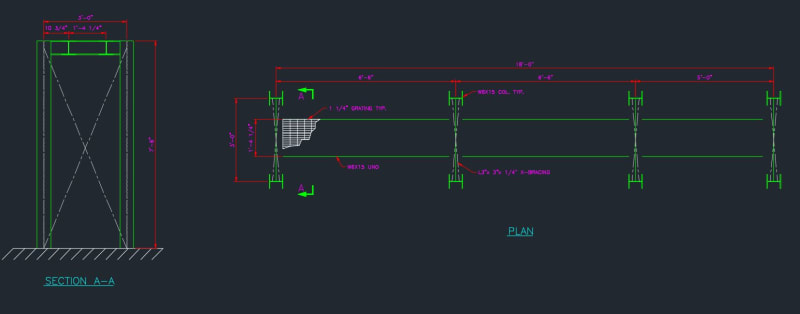