CosSin
Structural
- Feb 2, 2021
- 7
Can anyone help me in regards to the tendon design for rock anchors used in retaining wall?
I am using AS4678 and wondering what tensile strength fp below refer to? Is it breaking strength or yield strength?
I used yield strength but 3x15.2 tendons only gives me less than 500kN. In this case I wonder how other engineers use 3x15.2 (even just 2x15.2) tendons for 6m retaining walls where the tension is greater than 500kN easily?
I also want to clarify the concept of working load and proof load.
Say the design tension is 450kN and I am using 3x15.2 tendons with 470kN capacity (with fp = fpy for the above formula). Now the working load Pw as per AS4678 is 60% of its yield strength which is 386kN and proof load is 1.1*Pw = 425 kN which is lower than the design tension. Is it acceptable that the proof load is lower than ultimate design tension in anchor?
I am using AS4678 and wondering what tensile strength fp below refer to? Is it breaking strength or yield strength?
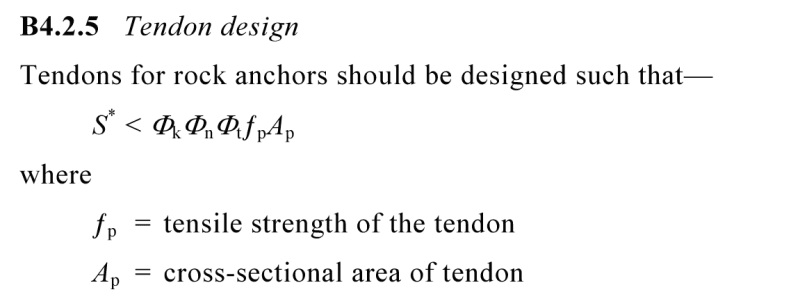
I used yield strength but 3x15.2 tendons only gives me less than 500kN. In this case I wonder how other engineers use 3x15.2 (even just 2x15.2) tendons for 6m retaining walls where the tension is greater than 500kN easily?
I also want to clarify the concept of working load and proof load.
Say the design tension is 450kN and I am using 3x15.2 tendons with 470kN capacity (with fp = fpy for the above formula). Now the working load Pw as per AS4678 is 60% of its yield strength which is 386kN and proof load is 1.1*Pw = 425 kN which is lower than the design tension. Is it acceptable that the proof load is lower than ultimate design tension in anchor?