Hello All,
During a recent inspection (St. Louis Area for reference) we noticed diagonals separated from top chord at peak/metal plate and are uncertain of why this happened. No recent construction activity or remodels. The resident of 40 years recently noticed the ceiling was sagging/drywall cracking. Let us know your input/opinion/experiences on causes of damage. Thanks!
During a recent inspection (St. Louis Area for reference) we noticed diagonals separated from top chord at peak/metal plate and are uncertain of why this happened. No recent construction activity or remodels. The resident of 40 years recently noticed the ceiling was sagging/drywall cracking. Let us know your input/opinion/experiences on causes of damage. Thanks!
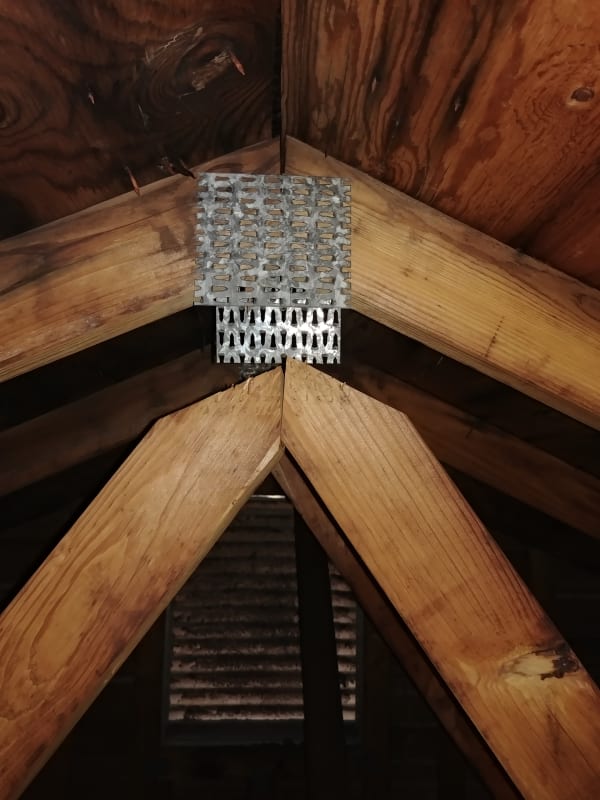
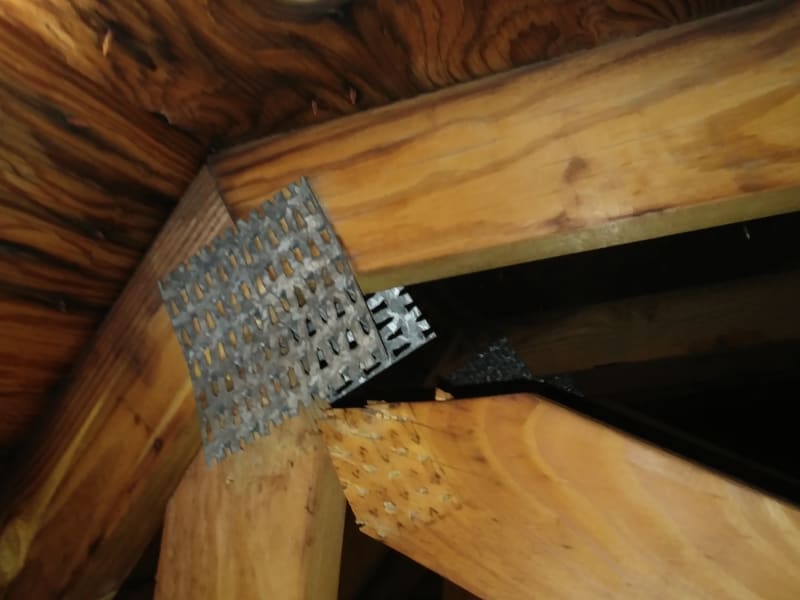