Vikas4auto2019
Mechanical
- Sep 23, 2019
- 13
hello guys,
PLEASE FIND THE IMAGE BELOW YTO UNDERSTAND MY QUESTION.
I just wanted to know that.. is there any empirical // calculative method to design the slot for (max) linear motion.
what are the parameters I need to get for these calculations?
Also, let me know what types of motion we can call it.
Thanks in advance.
PLEASE FIND THE IMAGE BELOW YTO UNDERSTAND MY QUESTION.
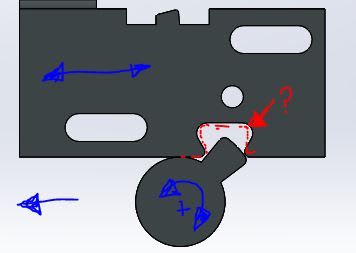
I just wanted to know that.. is there any empirical // calculative method to design the slot for (max) linear motion.
what are the parameters I need to get for these calculations?
Also, let me know what types of motion we can call it.
Thanks in advance.