Michael Lighting
Automotive
- Feb 2, 2020
- 4
Hi all
We manufacturer a light which seem to have an issue of rusting at one site. The stainless steel code is 316L, which has never had a problem but at this site we do. We've had to replace 10 lights and will have to do so again as the client is not happy with our equipment. I feel that the issue could be to do with their water purification, they have told me that they use Bromie to bring up the pH levels and to clean the water.
I am not sure if they use 100 % Bromine, but I think there could be other chemicals included in their mixture, I've asked them to send me the Chemical Compound used in the water. Would this have any effect on our product and if so what can I do to prevent the oxidation happening to our lights at this site.
Also the Pole on the left you can see has got the issue as well above and below, but photos can't be seen on this. I think they are using 304 stainless steel, but could be wrong.
I would Appreciate the help to resolve this issue.
We manufacturer a light which seem to have an issue of rusting at one site. The stainless steel code is 316L, which has never had a problem but at this site we do. We've had to replace 10 lights and will have to do so again as the client is not happy with our equipment. I feel that the issue could be to do with their water purification, they have told me that they use Bromie to bring up the pH levels and to clean the water.
I am not sure if they use 100 % Bromine, but I think there could be other chemicals included in their mixture, I've asked them to send me the Chemical Compound used in the water. Would this have any effect on our product and if so what can I do to prevent the oxidation happening to our lights at this site.
Also the Pole on the left you can see has got the issue as well above and below, but photos can't be seen on this. I think they are using 304 stainless steel, but could be wrong.
I would Appreciate the help to resolve this issue.
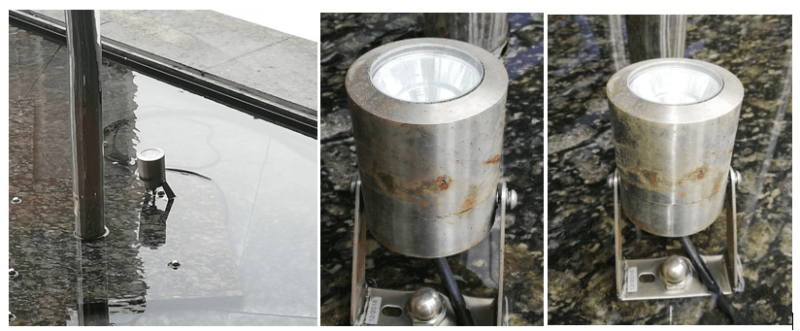