Deefer
Structural
- Mar 2, 2021
- 7
Hi Everyone. Safety and structural engineering question for you experts.
I'm designing a structural frame for an outdoor public art display. Two vertical steel cables will be tensioned from a horizontal metal rail down to concrete flooring 8 feet below. The two cables have about an 8" gap between them. Aluminum discs will be attached to the cables via four holes drilled into each disc. Here's a visualization of the frame, showing a series of the two-cable setup I've described.
I need some advice on making sure my cables and cable rigging are strong enough to withstand public interaction. This could take the form of a grown 240 pound man falling against or trying to jump onto the suspended aluminum discs. I was originally thinking a 500 pound working load for EACH cable would be sufficient, but am thinking that may not be enough. Whatever working load I settle on, I'll of course make sure my weakest link in the rigging can bear that load.
What are your expert thoughts on a safe working load to design for? I'll be monitoring this discussion to answer questions in case I left out significant details.
The frame uses 4" OD 11 gauge stainless steel tubing (but correct me if I'm wrong), so I'm pretty sure the frame will be strong enough. The cables need to be tensioned just enough so that the lines remain fairly taut when people try to mess with them. The aluminum discs are 14" and 18" wide x 1/8" thick.
Thanks in advance for helping improve public art. Folks in the materials engineering section were super helpful with aluminum/stainless corrosion.
I'm designing a structural frame for an outdoor public art display. Two vertical steel cables will be tensioned from a horizontal metal rail down to concrete flooring 8 feet below. The two cables have about an 8" gap between them. Aluminum discs will be attached to the cables via four holes drilled into each disc. Here's a visualization of the frame, showing a series of the two-cable setup I've described.
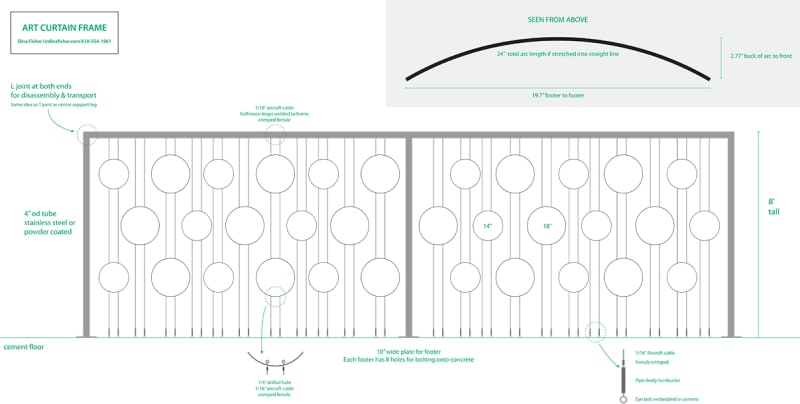
I need some advice on making sure my cables and cable rigging are strong enough to withstand public interaction. This could take the form of a grown 240 pound man falling against or trying to jump onto the suspended aluminum discs. I was originally thinking a 500 pound working load for EACH cable would be sufficient, but am thinking that may not be enough. Whatever working load I settle on, I'll of course make sure my weakest link in the rigging can bear that load.
What are your expert thoughts on a safe working load to design for? I'll be monitoring this discussion to answer questions in case I left out significant details.
The frame uses 4" OD 11 gauge stainless steel tubing (but correct me if I'm wrong), so I'm pretty sure the frame will be strong enough. The cables need to be tensioned just enough so that the lines remain fairly taut when people try to mess with them. The aluminum discs are 14" and 18" wide x 1/8" thick.
Thanks in advance for helping improve public art. Folks in the materials engineering section were super helpful with aluminum/stainless corrosion.