A client has decided against the external plate connection for a timber scissor truss and has requested concealed connection for the 90mm (3.5”) wide members.
What type of concealed connections are typically used for these truss? I was considering about plate connections for the top three connections, coach screws for bottom/chord connections. How are the bottom chords detailed where they cross? Note the truss is not very heavily loaded and is more decorative. Also, is there a rule of thumb of where the bottom chord should ideally insect the top chord - like mid-point?
What type of concealed connections are typically used for these truss? I was considering about plate connections for the top three connections, coach screws for bottom/chord connections. How are the bottom chords detailed where they cross? Note the truss is not very heavily loaded and is more decorative. Also, is there a rule of thumb of where the bottom chord should ideally insect the top chord - like mid-point?
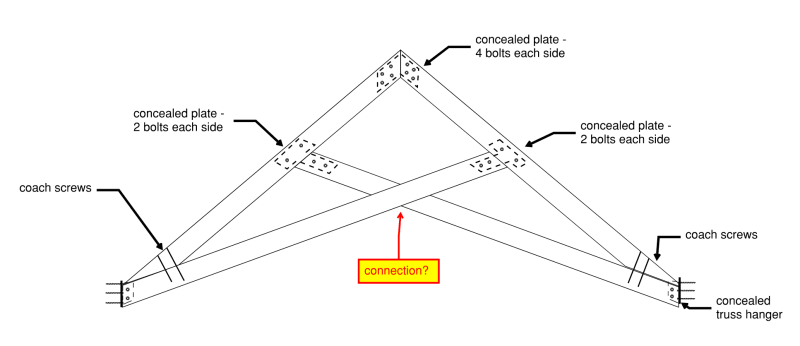