Hi all
In one of my 3D analysis, I have to compress a seal into a groove which is formed between 2 parts
First step is ok, push the ring into the groove
2nd step is to remove the "pusher", ok also
But the third step ... When I compress the upper part, at some point the contact "explodes" because the rubber extrudes into the groove
- Analysis is done using explicit solver (I attempted to do in in static this failed) with stable time increment to accelerate to calculation (but not too much)
- Rubber is neo hookean
- I tried all types of contact between the 2 parts (included general contact), same problem
- I tried ALE adaptative meshing with C3D8R elements for the seal, same problem
- Analysis is 3D, 36° sector with symmetry BC's
Any thoughts ?
Thanks
In one of my 3D analysis, I have to compress a seal into a groove which is formed between 2 parts
First step is ok, push the ring into the groove
2nd step is to remove the "pusher", ok also
But the third step ... When I compress the upper part, at some point the contact "explodes" because the rubber extrudes into the groove
- Analysis is done using explicit solver (I attempted to do in in static this failed) with stable time increment to accelerate to calculation (but not too much)
- Rubber is neo hookean
- I tried all types of contact between the 2 parts (included general contact), same problem
- I tried ALE adaptative meshing with C3D8R elements for the seal, same problem
- Analysis is 3D, 36° sector with symmetry BC's
Any thoughts ?
Thanks
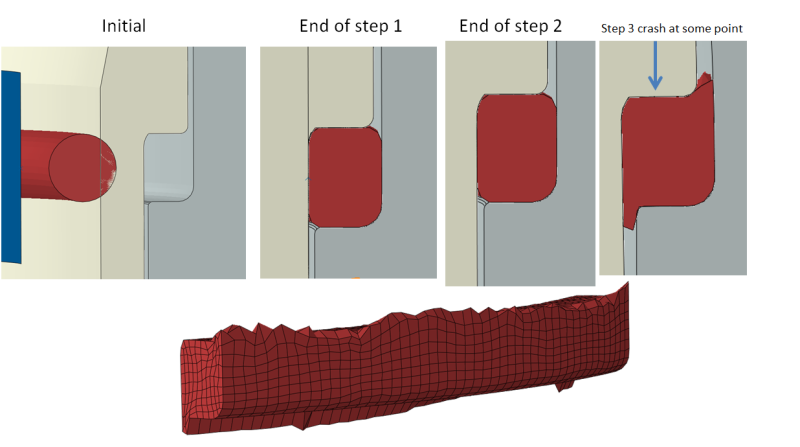