audiobeer
Electrical
- Mar 5, 2017
- 5
Some smart guys in here ![[thumbsup2] [thumbsup2] [thumbsup2]](/data/assets/smilies/thumbsup2.gif)
Was hoping for some advice - need to seal a stainless 316 pin (for electrical measurement) against 10 bar fluid pressure in plastic injection molded part (food safe e.g. PP).
See rubbish sketch I made with a few ideas. Pros and cons:
Option 1: insert molded straight pin - may leak as plastic shrinks, and insert mold tool more money plus more time (possible danger of damage to mold). But it's quite simple.
Option 2: insert molded with labyrinth features on pin - better as more surface area and longer fluid path so more resistance to leaking. But same issues with mold cost and part cost plus danger of leaking due to shrink still maybe.
Option 3: interference fit barbed pin into molded hole after part is made - simpler mold and no issue with plastic shrinkage just need to make sure pin doesn't come loose. Needs assembly after part is made and requires good tolerance on hole and pin (latter should be ok I guess).
Option 4: any of above with epoxy bead in chamfer or circular pocket - use epoxy that expands a little.
Any thoughts? Or other options?
![[thumbsup2] [thumbsup2] [thumbsup2]](/data/assets/smilies/thumbsup2.gif)
Was hoping for some advice - need to seal a stainless 316 pin (for electrical measurement) against 10 bar fluid pressure in plastic injection molded part (food safe e.g. PP).
See rubbish sketch I made with a few ideas. Pros and cons:
Option 1: insert molded straight pin - may leak as plastic shrinks, and insert mold tool more money plus more time (possible danger of damage to mold). But it's quite simple.
Option 2: insert molded with labyrinth features on pin - better as more surface area and longer fluid path so more resistance to leaking. But same issues with mold cost and part cost plus danger of leaking due to shrink still maybe.
Option 3: interference fit barbed pin into molded hole after part is made - simpler mold and no issue with plastic shrinkage just need to make sure pin doesn't come loose. Needs assembly after part is made and requires good tolerance on hole and pin (latter should be ok I guess).
Option 4: any of above with epoxy bead in chamfer or circular pocket - use epoxy that expands a little.
Any thoughts? Or other options?
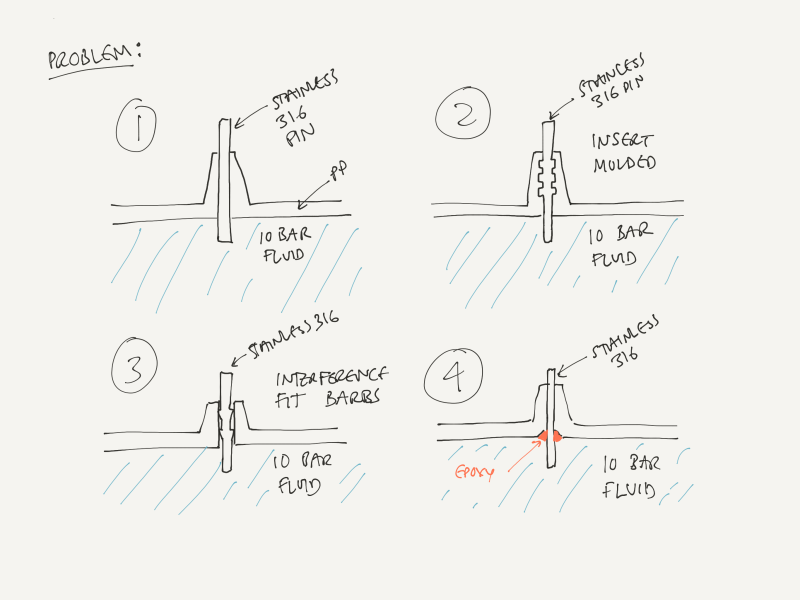