JTuhiwai
Mechanical
- Aug 2, 2023
- 1
Hi Team,
I'm reaching out to anyone that has worked on input of acoustic filler for a Stainless Steel Silencer.
We are wanting to fill a series of Cassettes with an acoustic absorbing material that can dampen sound.
I have populated process and design conditions below. We are wanting to put 316L swarf in these silencers
however we are trying to source an alternative solution for and looking for other options.
We have ruled out the use of Rockwool, and composite material fillers as the service is Geothermal
service and causes materials to degrade over time.
Design Criteria for the filler
• Density – 500kg/m3 maximum allowable density / m³
o Need to make sure its not absorbing water and becoming too heavy
• Temperature 100°C - 120°C
•
How much use it’ll have
o TH32 – 2 times a year maybe for a 12-24hrs each time
o Separation station – daily trim, smaller flow through it
8 hours of full use 4 times a year
Flow
o Steam impingement – 60m/s
o Small solids coming through (could break/damage small membranes)
• Corrosive environment
o Geothermal service – H2S & lots of other dissolved solids
• Dimensions for fitting into the panel
o Need a total volume of 56m3
o Height = 2400mm
o Thickness = 240mm
o Width= pretty variable but can cut to suit
Plan for install
• Filler Material will be inserted into the panels (TACG-MTL-3-000-MEC-DET-0127).
• Panels sealed off and installed into silencers.
Possible life expectancy of material filler 5 yrs.
Have attached reference of model and cassette drawings below.
I'm reaching out to anyone that has worked on input of acoustic filler for a Stainless Steel Silencer.
We are wanting to fill a series of Cassettes with an acoustic absorbing material that can dampen sound.
I have populated process and design conditions below. We are wanting to put 316L swarf in these silencers
however we are trying to source an alternative solution for and looking for other options.
We have ruled out the use of Rockwool, and composite material fillers as the service is Geothermal
service and causes materials to degrade over time.
Design Criteria for the filler
• Density – 500kg/m3 maximum allowable density / m³
o Need to make sure its not absorbing water and becoming too heavy
• Temperature 100°C - 120°C
•
How much use it’ll have
o TH32 – 2 times a year maybe for a 12-24hrs each time
o Separation station – daily trim, smaller flow through it
8 hours of full use 4 times a year
Flow
o Steam impingement – 60m/s
o Small solids coming through (could break/damage small membranes)
• Corrosive environment
o Geothermal service – H2S & lots of other dissolved solids
• Dimensions for fitting into the panel
o Need a total volume of 56m3
o Height = 2400mm
o Thickness = 240mm
o Width= pretty variable but can cut to suit
Plan for install
• Filler Material will be inserted into the panels (TACG-MTL-3-000-MEC-DET-0127).
• Panels sealed off and installed into silencers.
Possible life expectancy of material filler 5 yrs.
Have attached reference of model and cassette drawings below.
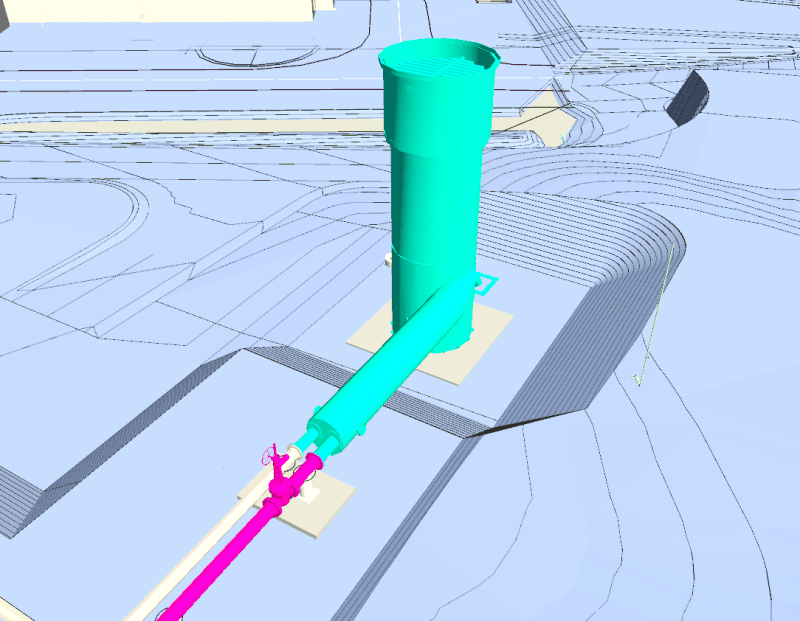
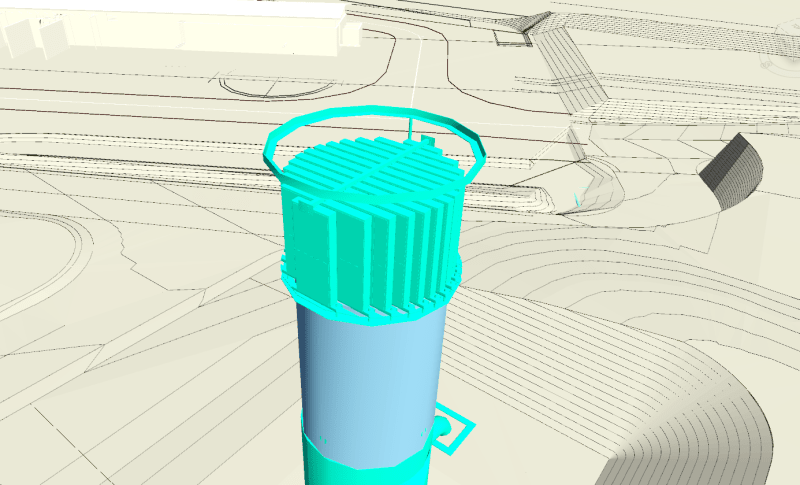
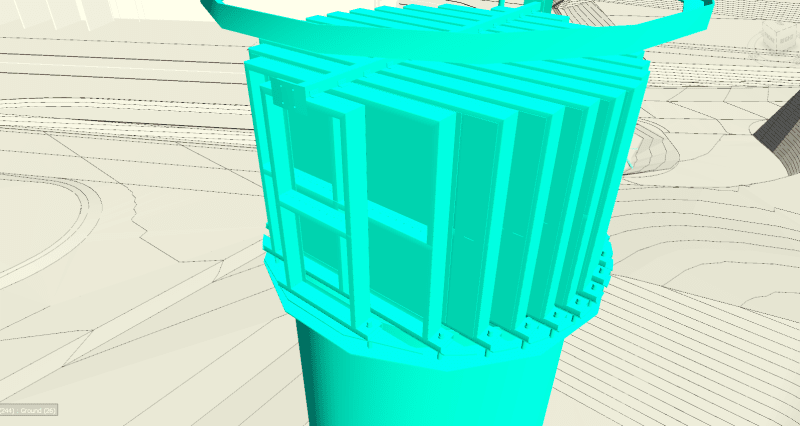