tommj
Industrial
- May 4, 2020
- 30
Dodge 3.6L v6, flex plate centers break out. The steel center is like glass. The one shown replaced the first one that failed in the same manner 4 years ago and was supposed to be an improved part. All are MOPAR OEM parts, current failure at 174k mi. The part is cheap but costs $600 in labor to get to. What are they doing wrong? Should this be annealed or otherwise heat treated to improve longevity? This didn't happen 20 years ago....
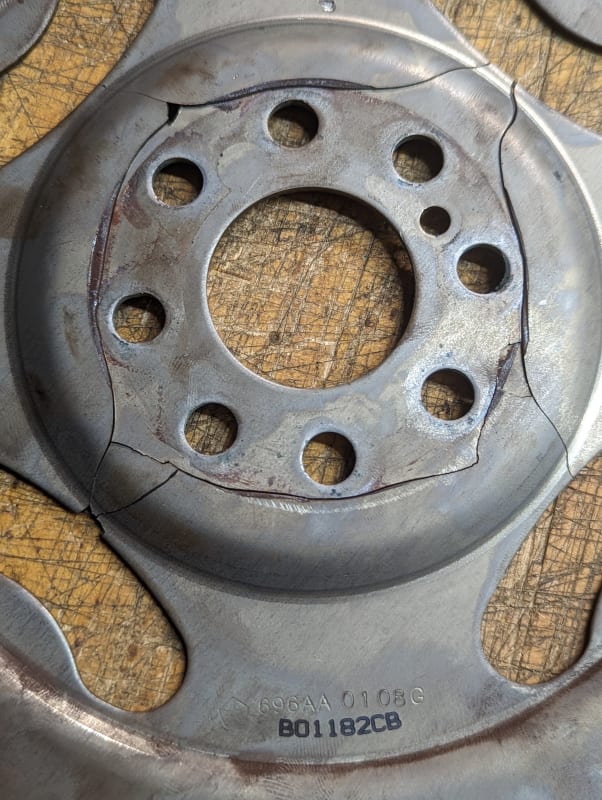
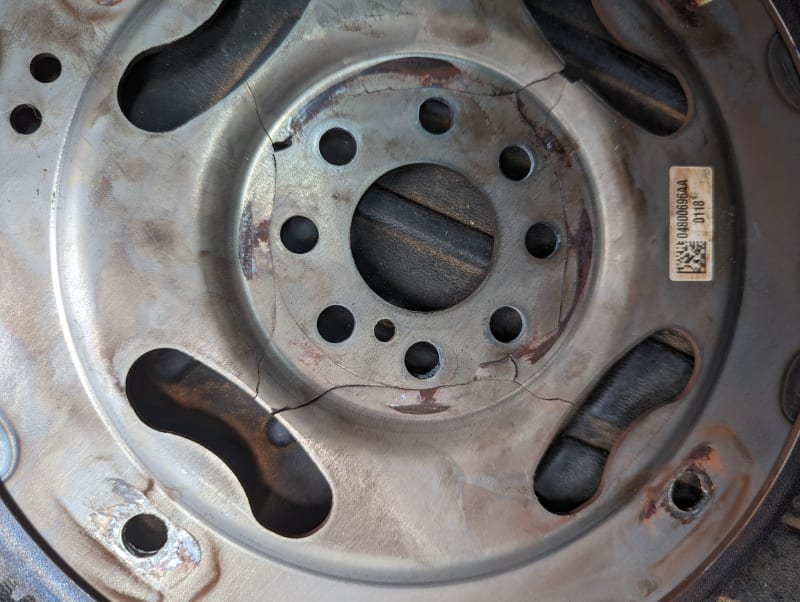
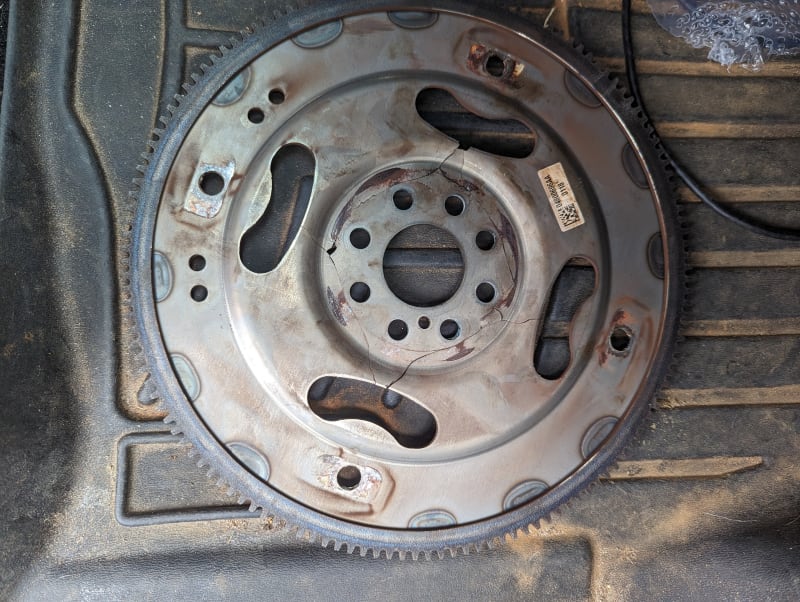