I am looking for clarification on alignments when a datum axis or center point has precedence before a datum plane or line in a DRF, especially when the plane/ line is offset to the center point or axis
According to the standards I see for 2009/2018, the plane or line datum simulator progresses from MMB to LMB to make full contact with the feature like illustrated in Figure 7-34 below.
However if there would be no tolerance on datum B in the example would the simulator keep progressing until the feature is fully parallel with the datum reference frame?
How would I properly gage the part in the example below? Datum C does not have a position or profile tolerance to AB. Would I just make datum feature C parallel to the DRF or would I make the datum simulator at Nominal and rotate C around B until the high points touch the simulator?
According to the standards I see for 2009/2018, the plane or line datum simulator progresses from MMB to LMB to make full contact with the feature like illustrated in Figure 7-34 below.
However if there would be no tolerance on datum B in the example would the simulator keep progressing until the feature is fully parallel with the datum reference frame?
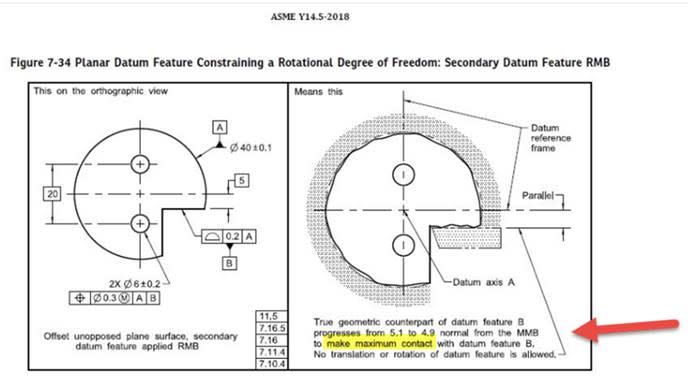
How would I properly gage the part in the example below? Datum C does not have a position or profile tolerance to AB. Would I just make datum feature C parallel to the DRF or would I make the datum simulator at Nominal and rotate C around B until the high points touch the simulator?
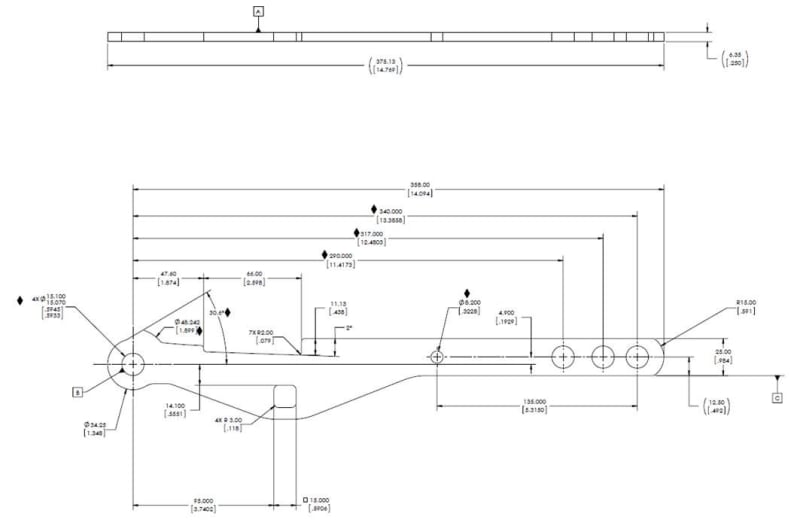