Hi Everyone,
We are reinforcing a corroded existing W16x36 with two centred C12x30 channels.
I would like your opinion on how to determine the efforts on the connection bolts and their spacing as the shear flow is null. I detemined the maximum force from the stress on the half top of the channels, and I'm not sure on many longitudinal bolt I should divide it.
And do we have to provide a clamp load from the bolts, how to calculate it in this case ? do the bolts need to be pretentioned ?
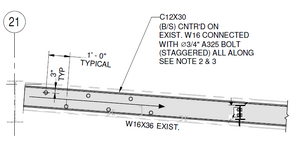
Thank you for your help.
We are reinforcing a corroded existing W16x36 with two centred C12x30 channels.
I would like your opinion on how to determine the efforts on the connection bolts and their spacing as the shear flow is null. I detemined the maximum force from the stress on the half top of the channels, and I'm not sure on many longitudinal bolt I should divide it.
And do we have to provide a clamp load from the bolts, how to calculate it in this case ? do the bolts need to be pretentioned ?
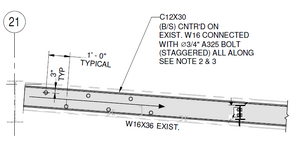
Thank you for your help.