I'm a technician at a powerplant working with one of my supervisors in an effort to save money on our cooling tower chemicals and improve our process. We currently spend roughly 250k per year on scale & corrosion inhibitors using a phosphoric acid as a corrosion inhibitor and HEDP for scale inhibitor - both are fed simultaneously around the clock. (Our facility has never faced issues with either phenomenon, but have always utilized both types of chemicals).
The question I have is, can a calculated LSI or other 'scale tendency' formula really be used to determine if our cooling tower circulated water is corrosive or scale forming -- Thus necessary to feed either the scale or corrosion inhibitors? -- and is there any 'dead band' in this range -- (For instance, using LSI, if we were to stay between -.2 and .2, do we need either chemical? -- do we need both?)
Our site has instrumentation on the circulating water for Temperature, pH, Conductivity, Alkalinity, and Calcium. We also monitor and control the make-up water pH, monitor the make-up conductivity, and monitor/control the free chlorine.
The doubts I have are from studies which suggest that 'all circulating water' is corrosive due to dissolved oxygen, web sites stating that water with an LSI between 0 and 0.3 can still be corrosive, -0.3 and 0 can be scale forming, ect. The fact that given the same chemistry values, LSI says the water is safe when the RSI calculation says the water is aggressive, ect.
I guess the real question I have is, can I use a calculated LSI number from our instrumentation to determine if our facility needs to be feeding a scale or corrosion inhibitor? Below is a simplified paint drawing of the system.
The question I have is, can a calculated LSI or other 'scale tendency' formula really be used to determine if our cooling tower circulated water is corrosive or scale forming -- Thus necessary to feed either the scale or corrosion inhibitors? -- and is there any 'dead band' in this range -- (For instance, using LSI, if we were to stay between -.2 and .2, do we need either chemical? -- do we need both?)
Our site has instrumentation on the circulating water for Temperature, pH, Conductivity, Alkalinity, and Calcium. We also monitor and control the make-up water pH, monitor the make-up conductivity, and monitor/control the free chlorine.
The doubts I have are from studies which suggest that 'all circulating water' is corrosive due to dissolved oxygen, web sites stating that water with an LSI between 0 and 0.3 can still be corrosive, -0.3 and 0 can be scale forming, ect. The fact that given the same chemistry values, LSI says the water is safe when the RSI calculation says the water is aggressive, ect.
I guess the real question I have is, can I use a calculated LSI number from our instrumentation to determine if our facility needs to be feeding a scale or corrosion inhibitor? Below is a simplified paint drawing of the system.
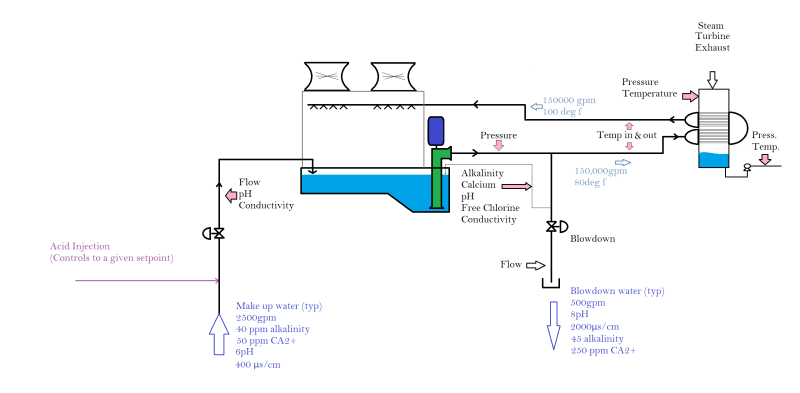