Calvin Murphy
Aerospace
- Nov 22, 2024
- 16
Hello everyone,
I'm new to this site, and I'm hoping to find anyone who has experience with launch adapter rings (LAR) or their installation.
If you can answer any of the questions below, please reply or message me.
All pictures are from publicly available payload user interface guides.
Picture of LAR pair and clamp-band for context:
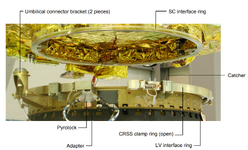
Cross sections of some sizes of LAR:
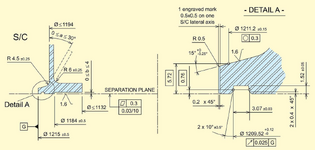
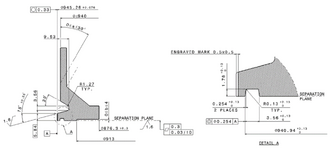
I'm new to this site, and I'm hoping to find anyone who has experience with launch adapter rings (LAR) or their installation.
If you can answer any of the questions below, please reply or message me.
- How common is it for components on the satellite to be located within the inner diameter of the LAR?
- Are there consistent guidelines for where those components can be located within the LAR on the satellite?
- How common is it for LARs to be insulated with MLI or foil, and how much of the LAR is guaranteed to be exposed?
- During installation, are they coated in any lubrication that might still be present in space?
- Are the LAR's manufactured by launch providers and left to clients to install, or are clients responsible for designing their own LARs that will interlock with the one on the rocket?
- Is there a way to track which LAR shapes and sizes are in space currently?
All pictures are from publicly available payload user interface guides.
Picture of LAR pair and clamp-band for context:
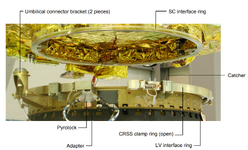
Cross sections of some sizes of LAR:
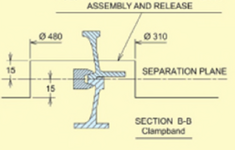
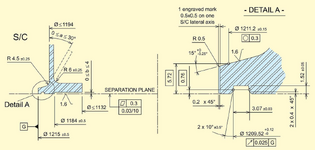
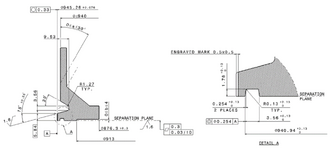