Vaishnav Bhaskaran
Student
- Feb 28, 2023
- 3
Hello,
I am modelling a plate with a hole in it, subjected to a compressive displacement load. There is an overlap of elements when the hole is compressed and I tried imposing a self-contact to the whole plate but the overlap still occurs. My model is a 3D part with shell elements. I tried reducing the model to 2D and used solid elements which seem to reduce the overlap to some extent. I have a few questions here and would be really great if someone could help me
[ol 1]
[li]Is reducing the model to 2D is the only way to avoid this overlap? Is this a right approach?[/li]
[li]Am I applying self-contact correctly or am I missing something?[/li]
[li]Why can't 3D shell edges be used to apply self-contact?[/li]
[/ol]
I also found a similar thread in this forum but there the issue was non-convergence. In my case I am getting solutions for different load cases but I am stuck with the overlap.
Thanks in advance!
Regards,
Vaishnav
Fig.1 Base Model with BC. The model is ZSYMM
Fig.2 3D model with overlap of elements in the top region of the hole
Fig.3 2D model with solid elements with much less overlap
I am modelling a plate with a hole in it, subjected to a compressive displacement load. There is an overlap of elements when the hole is compressed and I tried imposing a self-contact to the whole plate but the overlap still occurs. My model is a 3D part with shell elements. I tried reducing the model to 2D and used solid elements which seem to reduce the overlap to some extent. I have a few questions here and would be really great if someone could help me
[ol 1]
[li]Is reducing the model to 2D is the only way to avoid this overlap? Is this a right approach?[/li]
[li]Am I applying self-contact correctly or am I missing something?[/li]
[li]Why can't 3D shell edges be used to apply self-contact?[/li]
[/ol]
I also found a similar thread in this forum but there the issue was non-convergence. In my case I am getting solutions for different load cases but I am stuck with the overlap.
Thanks in advance!
Regards,
Vaishnav
Fig.1 Base Model with BC. The model is ZSYMM
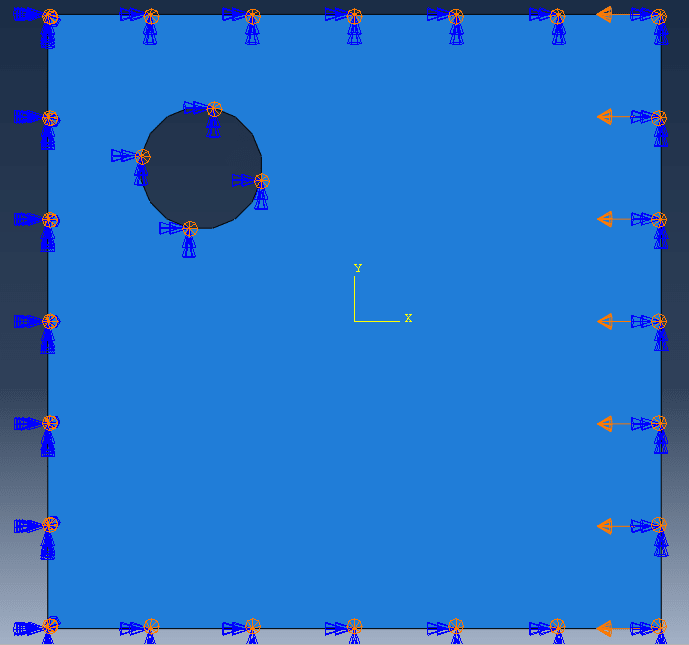
Fig.2 3D model with overlap of elements in the top region of the hole
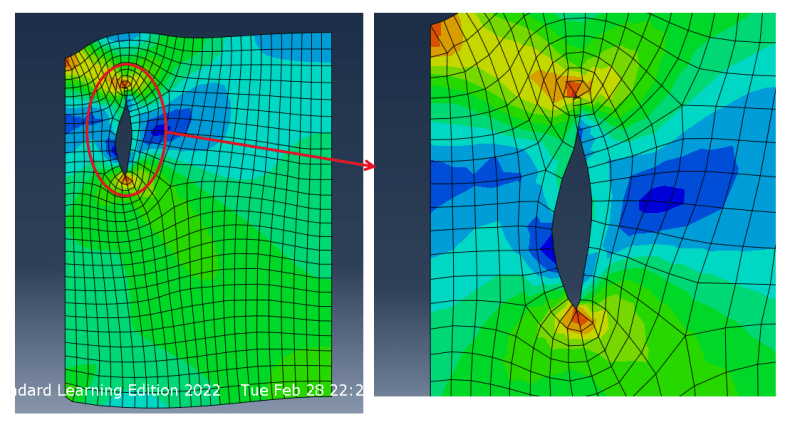
Fig.3 2D model with solid elements with much less overlap
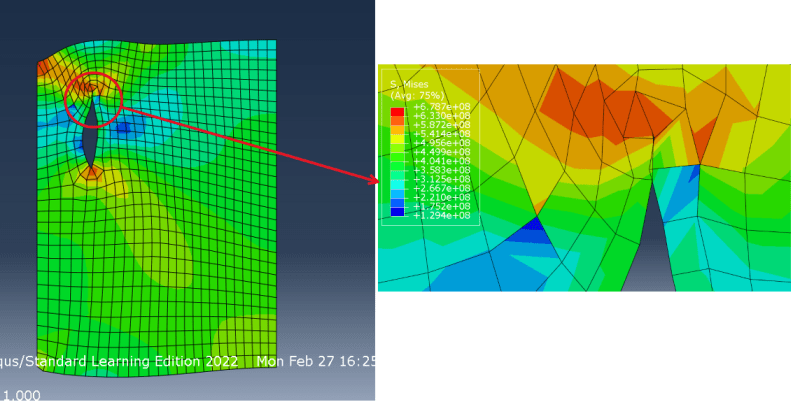