JoelTXCive
Civil/Environmental
I'm designing the anchor bolts for a self contained sluice gate with a motor controlled actuator.
These are 10x10 gates that have a self weight around 20 kips. The stall load of the 7.5hp motor is 300 kips due to all the mechanical advantage of the actuator's gearbox.
I have the tension/compression loads due to water pressure worked out, but have a question regarding how the gate load is transferred to the supporting structure.
This morning, a mechanical engineer told me the self contained gate sends no load to the supporting structure other than self weight.
I agree with this statement for normal operations; but not for a 'stuck gate' scenario.
Normal Operation
Under normal operation, the self weight of the gate is carried by the anchor bolts in shear. When the motor turns on the stem is in tension and the yoke beam receives a point load. Neglecting friction, the net load to the anchor bolts does not change.
'Stuck Gate' Situation
If the gate gets hung up; then the motor will continue to pull until it reaches the stall load.
Assuming nothing breaks in the gate; the full stall load (300 kips) will get sent to the anchor bolts.
In my mind, the gate frame will attempt to close up like a clam shell in this condition. The full 300 kips will be carried in shear by the anchor bolts.
Question (or Confirmation of my logic)
Do I need to design the anchor bolts to handle the full stall load of the motor?
Or, is my logic wrong; and no load gets sent to the structure?
Thank you in advance.
These are 10x10 gates that have a self weight around 20 kips. The stall load of the 7.5hp motor is 300 kips due to all the mechanical advantage of the actuator's gearbox.
I have the tension/compression loads due to water pressure worked out, but have a question regarding how the gate load is transferred to the supporting structure.
This morning, a mechanical engineer told me the self contained gate sends no load to the supporting structure other than self weight.
I agree with this statement for normal operations; but not for a 'stuck gate' scenario.
Normal Operation
Under normal operation, the self weight of the gate is carried by the anchor bolts in shear. When the motor turns on the stem is in tension and the yoke beam receives a point load. Neglecting friction, the net load to the anchor bolts does not change.
'Stuck Gate' Situation
If the gate gets hung up; then the motor will continue to pull until it reaches the stall load.
Assuming nothing breaks in the gate; the full stall load (300 kips) will get sent to the anchor bolts.
In my mind, the gate frame will attempt to close up like a clam shell in this condition. The full 300 kips will be carried in shear by the anchor bolts.
Question (or Confirmation of my logic)
Do I need to design the anchor bolts to handle the full stall load of the motor?
Or, is my logic wrong; and no load gets sent to the structure?
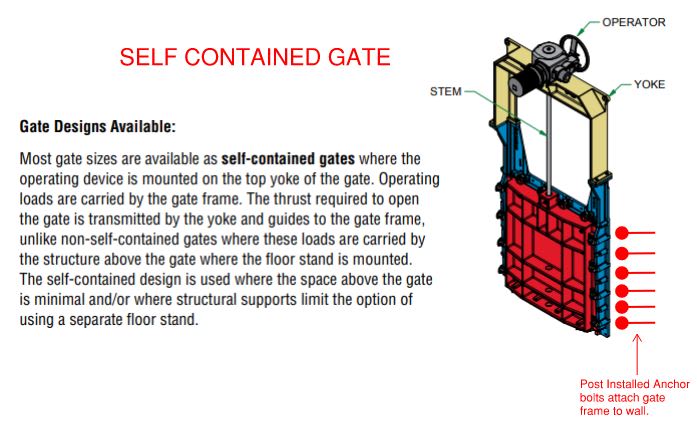
Thank you in advance.