mech_eng_p
Industrial
Hi.
I am trying to calculate a flat shaft cover, mounted with several bolts.
These are the dimensions (in metric system):
shaftØ140mm
cover outer D=160mm
thickness=12mm
bolt= M16 (3x), hole Ø18mm, pretension bolts is 640*70%MPa.
PCD=Ø110mm
First I tried doing this with the use of Roark formulas for stress and strain (Chapter 11, case 9a).
The results was a bendingstress at the centre of the plate of about 395 MPa.
For some reason, i wasn't expecting this high stresses, so i did a FEM analysis.
Pivot support, 3x 70300N (pre)tension.
With the following results: Maximum stress at centre plate about 150MPa.
This is indeed a huge difference.
I was assuming that using the uniform load of roark was a good idea, but maybe it was not.
Unfortunately i haven't found any other useful calculation to calculate the stress in a shaft cover (with holes).
Can anybody help me finding this?
Thanks!
I am trying to calculate a flat shaft cover, mounted with several bolts.
These are the dimensions (in metric system):
shaftØ140mm
cover outer D=160mm
thickness=12mm
bolt= M16 (3x), hole Ø18mm, pretension bolts is 640*70%MPa.
PCD=Ø110mm
First I tried doing this with the use of Roark formulas for stress and strain (Chapter 11, case 9a).
The results was a bendingstress at the centre of the plate of about 395 MPa.
For some reason, i wasn't expecting this high stresses, so i did a FEM analysis.
Pivot support, 3x 70300N (pre)tension.
With the following results: Maximum stress at centre plate about 150MPa.
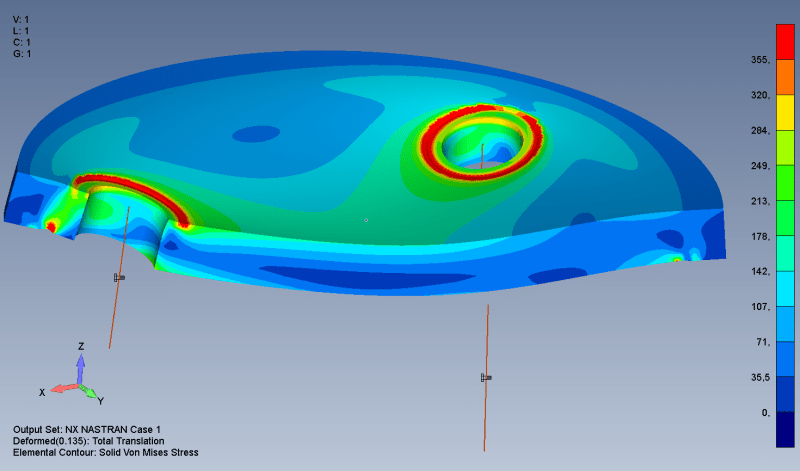
This is indeed a huge difference.
I was assuming that using the uniform load of roark was a good idea, but maybe it was not.
Unfortunately i haven't found any other useful calculation to calculate the stress in a shaft cover (with holes).
Can anybody help me finding this?
Thanks!