Hi All!
I'm designing for a strip of metal (b=11, h=1.48mm) to fail in shear. Its a pyro safety switch where a piston is forced to shear the strip and bend the flap of metal to create distance between the two pieces. I want to find the shear stress for a given force. I have attached an image of my analysis. I am not sure if I can simply assume the reaction forces act at the end of the supports or if I need to use a "distributed load" for the reaction forces (take the force to act at center of load). This gives different shear force diagrams so I was wondering which would be more correct. I am looking to use Tau=Vq/IT or would average shear Tau=V/A suffice? Thanks in advance.
I'm designing for a strip of metal (b=11, h=1.48mm) to fail in shear. Its a pyro safety switch where a piston is forced to shear the strip and bend the flap of metal to create distance between the two pieces. I want to find the shear stress for a given force. I have attached an image of my analysis. I am not sure if I can simply assume the reaction forces act at the end of the supports or if I need to use a "distributed load" for the reaction forces (take the force to act at center of load). This gives different shear force diagrams so I was wondering which would be more correct. I am looking to use Tau=Vq/IT or would average shear Tau=V/A suffice? Thanks in advance.
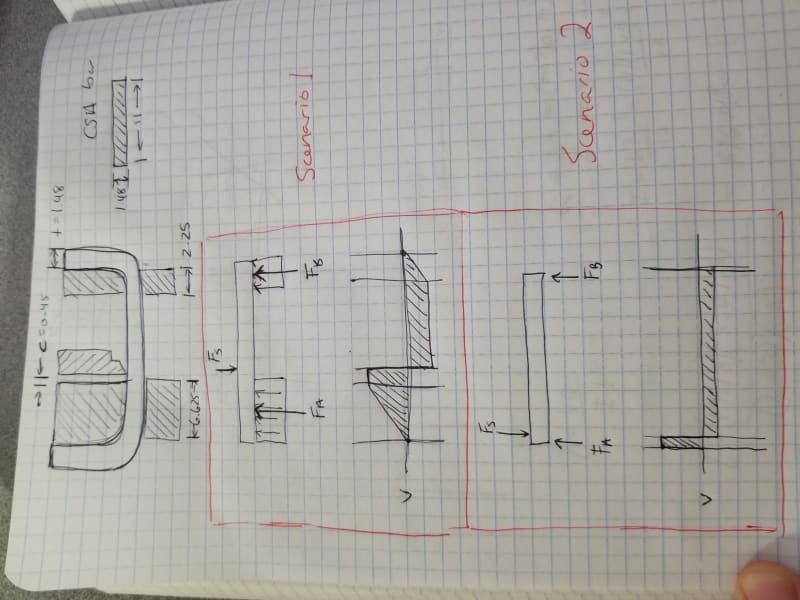