Hi All,
I have a problem where I want to calculate the shear flow in a built up beam where an existing beam will be strengthened by connecting another section to it (in this case the 7"x3" channel will be strengthened by connecting 125x65mm PFC section). See the figure below.
The proposal is to connect the 125x65 PFC to 7"x3" channel by using 1no. bolt at the middle (at neutral axis).
My question is, in order to carry out the shear flow calculation, we have to consider the connected section (125x75PFC) above the neutral axis. Hence the area to be calculated will be the half the area of the 125x65 section. The first moment of area then will be Q = A.y where y is going to be the distance from the neutral axis to the centroid of the half the 125x65 section (see in the figure below). In this case, do we calculate the shear flow like this, than compare it to the capacity of the bolt and work out how many bolts I need at what spacing? Or, since the bolt is connected at the neutral axis, the shear flow calculation has to be carried out at that location, where the Q will come out to be 0 due to the fact that distance from the neutral axis is 0?
Or it doesn't matter whether the bolt is connected (whether it's at the neutral axis or slightly above neutral axis)?
It would be great if someone can provide some clarifications on this problem.
I have a problem where I want to calculate the shear flow in a built up beam where an existing beam will be strengthened by connecting another section to it (in this case the 7"x3" channel will be strengthened by connecting 125x65mm PFC section). See the figure below.
The proposal is to connect the 125x65 PFC to 7"x3" channel by using 1no. bolt at the middle (at neutral axis).
My question is, in order to carry out the shear flow calculation, we have to consider the connected section (125x75PFC) above the neutral axis. Hence the area to be calculated will be the half the area of the 125x65 section. The first moment of area then will be Q = A.y where y is going to be the distance from the neutral axis to the centroid of the half the 125x65 section (see in the figure below). In this case, do we calculate the shear flow like this, than compare it to the capacity of the bolt and work out how many bolts I need at what spacing? Or, since the bolt is connected at the neutral axis, the shear flow calculation has to be carried out at that location, where the Q will come out to be 0 due to the fact that distance from the neutral axis is 0?
Or it doesn't matter whether the bolt is connected (whether it's at the neutral axis or slightly above neutral axis)?
It would be great if someone can provide some clarifications on this problem.
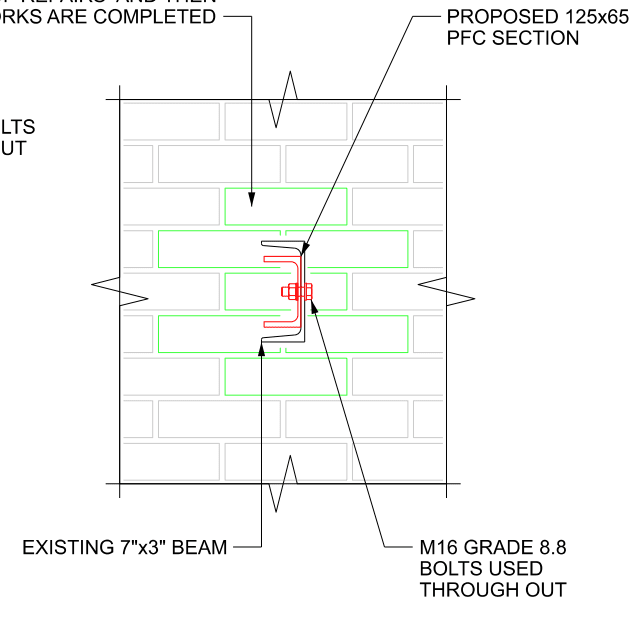
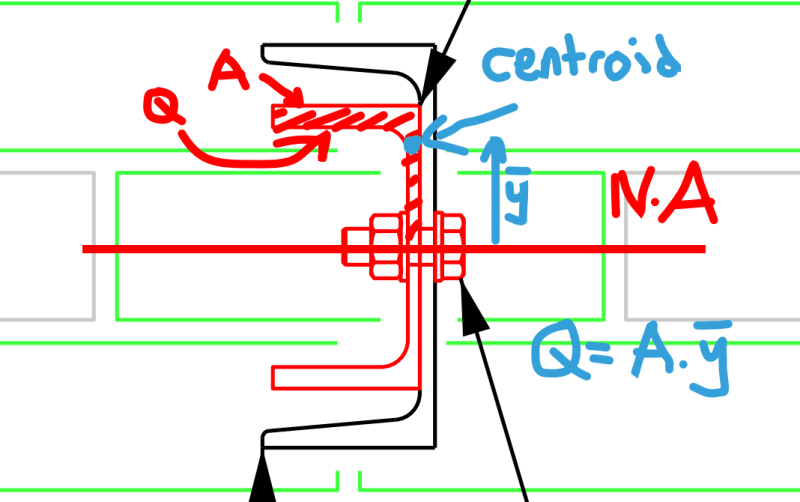