I will fully admit to being rusty on the subject since I don't deal with it (hardly ever) and it's been a long time since school...
If I have a soldier pile (W-beam) with a hole in it for a tieback, and I want to reinforce the flanges to make up for the loss of the section at the hole, I would intuitively solve for a flange force. To do this, I would use Moment / Depth (measured to the weld line) and then size the reinforcing plate and the weld to resist that flange force.
However, we have received comments from the AHJ that our plates are too long and they recommend using a shear flow equation like the one shown in the link below:
Which approach would you use and why? And, what am I missing in my logic of using M / d?
For the sake of the detail, I would assume you get no axial resistance from the web as it's been scarfed out to insert a pipe.
If I have a soldier pile (W-beam) with a hole in it for a tieback, and I want to reinforce the flanges to make up for the loss of the section at the hole, I would intuitively solve for a flange force. To do this, I would use Moment / Depth (measured to the weld line) and then size the reinforcing plate and the weld to resist that flange force.
However, we have received comments from the AHJ that our plates are too long and they recommend using a shear flow equation like the one shown in the link below:
Which approach would you use and why? And, what am I missing in my logic of using M / d?
For the sake of the detail, I would assume you get no axial resistance from the web as it's been scarfed out to insert a pipe.
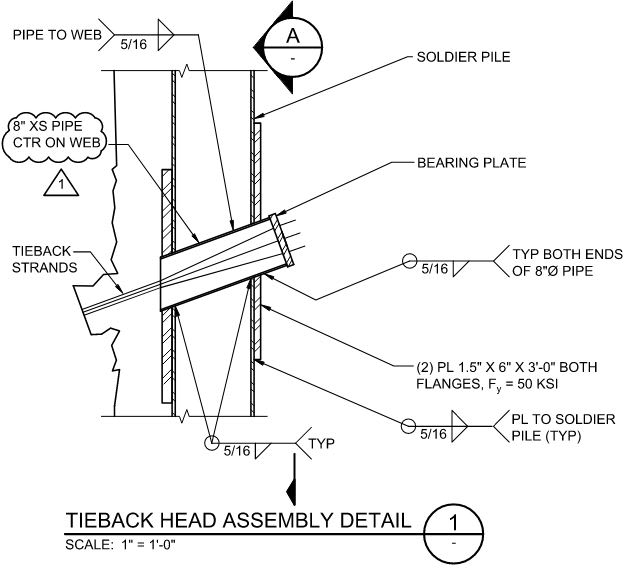