canmecheng
Mechanical
Hello,
How is shear load transferred from a bearing housing to a structure when using a bolted flange connection that has a tight fit? Is the shear load transferred assuming a non-slip connection generated by the bolt clamping force, or does the shear load transfer from mating surfaces which have a tight fit between the bearing housing and structure.
In my application, I am adding using a radial bearing to allow a table top to rotate. The bearing housing is attached to the fixed structure with a circular bolted flange. The flange of the supporting structure has a recess with a clearance fit H8g7. The operating speeds are low at 7rpm and I don't have any axial loading.
Thanks in advance.
How is shear load transferred from a bearing housing to a structure when using a bolted flange connection that has a tight fit? Is the shear load transferred assuming a non-slip connection generated by the bolt clamping force, or does the shear load transfer from mating surfaces which have a tight fit between the bearing housing and structure.
In my application, I am adding using a radial bearing to allow a table top to rotate. The bearing housing is attached to the fixed structure with a circular bolted flange. The flange of the supporting structure has a recess with a clearance fit H8g7. The operating speeds are low at 7rpm and I don't have any axial loading.
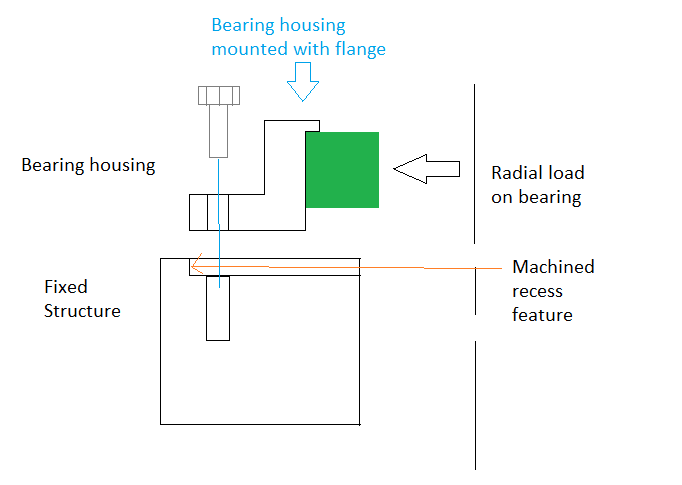
Thanks in advance.