Hi all,
I am connecting a steel beam to a concrete column and having a shear lug to take the huge shear forces from gravity loadings.
I am designing the shear lug as per ACI 349, the code does not discuss the checks of the shear lug incase the force is parallel to the edge (not perpendicular). However, going through ACI 318-11 appendix D, it says for anchor bolts '' The case of shear force parallel to an edge is shown in Fig. RD.6.2.1(c). The maximum shear force that can be applied parallel to the edge, V||, as governed by concrete breakout, is twice the maximum shear force that can be applied perpendicular to the edge, V⊥''.
My question is does this apply also to the shear lug case? Also, can i use the same special reinforcement specified in ACI 318 appendix D to resist the breakout around the lugs? How and what is the breakout perimeter?
Thanks in Advance
I am connecting a steel beam to a concrete column and having a shear lug to take the huge shear forces from gravity loadings.
I am designing the shear lug as per ACI 349, the code does not discuss the checks of the shear lug incase the force is parallel to the edge (not perpendicular). However, going through ACI 318-11 appendix D, it says for anchor bolts '' The case of shear force parallel to an edge is shown in Fig. RD.6.2.1(c). The maximum shear force that can be applied parallel to the edge, V||, as governed by concrete breakout, is twice the maximum shear force that can be applied perpendicular to the edge, V⊥''.
My question is does this apply also to the shear lug case? Also, can i use the same special reinforcement specified in ACI 318 appendix D to resist the breakout around the lugs? How and what is the breakout perimeter?
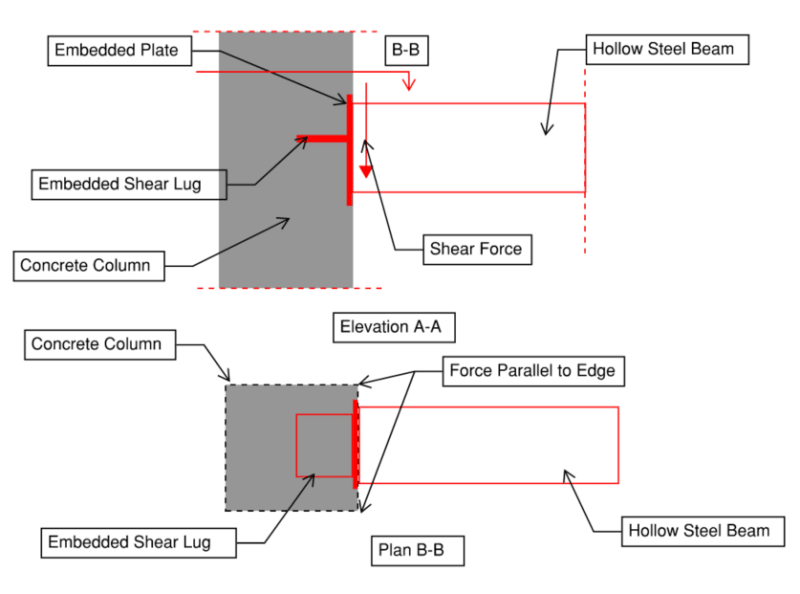
Thanks in Advance