I want to discuss about shear reinforcement - vertical stirrups.
Based on Eurocode 2, shear capacity of RC elements are based on 2d truss model as shown in picture bellow.
Because of vertical shear forces we have stirrups in tension.
In case we are making a composite (existing concrete + new concrete) and we use the same stirrups as connectors/dowels we are also having a horizontal shear forces on stirrups (because of a horizontal shear flow between both concrete elements).
I was reading a similar topic not long ago about that and some of you suggested that there is no interaction between shear-tension forces in a stirrup/rebar but I kinda disagree.
Anyway... Horizontal shear forces on a single stirrup is based on geometry, vertical forces and spacing between them.
But Im wondering how can I get a tension forces in a single stirrup on a 2d truss model from knowing what is the max bending moment and max shear force in a beam?
I know how to consider bending moments (N+ = N- = Md/z) but I dont know how to consider vertical reaction (shear forces) on a truss model.
To make things clear - I want to know how to get a tension force in a single stirrup based on bending/shear diagram.
I need this so I can make interaction shear - tension.
Based on Eurocode 2, shear capacity of RC elements are based on 2d truss model as shown in picture bellow.
Because of vertical shear forces we have stirrups in tension.
In case we are making a composite (existing concrete + new concrete) and we use the same stirrups as connectors/dowels we are also having a horizontal shear forces on stirrups (because of a horizontal shear flow between both concrete elements).
I was reading a similar topic not long ago about that and some of you suggested that there is no interaction between shear-tension forces in a stirrup/rebar but I kinda disagree.
Anyway... Horizontal shear forces on a single stirrup is based on geometry, vertical forces and spacing between them.
But Im wondering how can I get a tension forces in a single stirrup on a 2d truss model from knowing what is the max bending moment and max shear force in a beam?
I know how to consider bending moments (N+ = N- = Md/z) but I dont know how to consider vertical reaction (shear forces) on a truss model.
To make things clear - I want to know how to get a tension force in a single stirrup based on bending/shear diagram.
I need this so I can make interaction shear - tension.
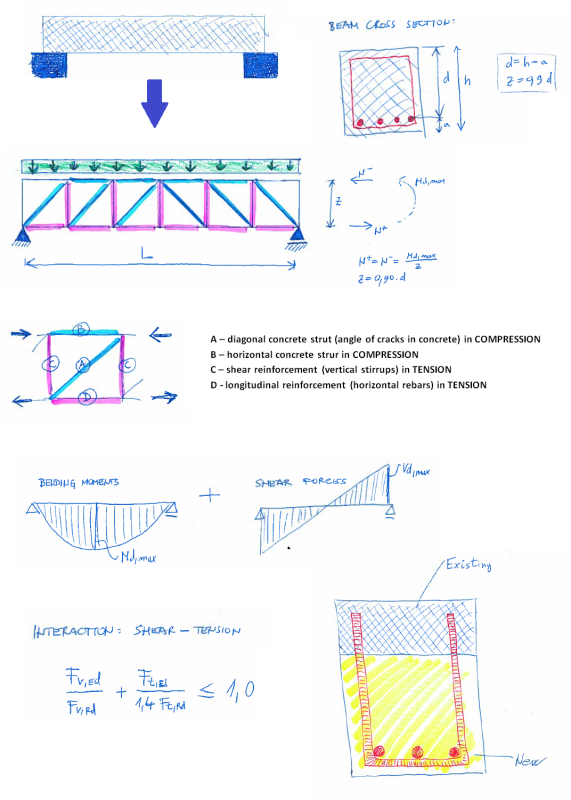