CDLD
Structural
- May 20, 2020
- 224
I've got a small column pier (9" high) sitting on an 8" elevated slab (dowels post-installed into slab).
Curious how others justify shear transfer at the slab/pier joint?
In a normal pier/footing case, I would develop the bars above/below the pier/footing joint and use the shear friction clauses in ACI.
Since I don't have adequate development length into the slab, would it be acceptable to assume the bottom tie transfers shear equally to the 4 pier vertical bars and design them as dowels into the slab (using concrete breakout clauses)?
Can you design the 4 vertical pier bars as anchors (with shear and tension component) and check for breakout from the slab.
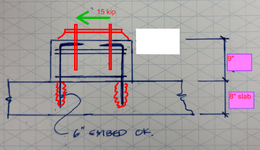
Curious how others justify shear transfer at the slab/pier joint?
In a normal pier/footing case, I would develop the bars above/below the pier/footing joint and use the shear friction clauses in ACI.
Since I don't have adequate development length into the slab, would it be acceptable to assume the bottom tie transfers shear equally to the 4 pier vertical bars and design them as dowels into the slab (using concrete breakout clauses)?
Can you design the 4 vertical pier bars as anchors (with shear and tension component) and check for breakout from the slab.
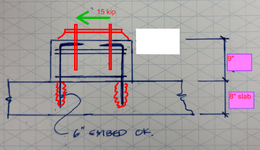