By believing I should seek precision in my model (20 story building with small floor area), I opened a pandora box and I don't know how to proceed.
I know the majority model their superstructure with supports as pinned/fixed even if there are piles beneath, but I figured out that maybe by modeling the piles I can simplify further tasks like pile design and mat foundation. The problem is that I have now very large deflections and very large moments on the shear walls. I don't know what to do with these forces. Should I revert to the model with pinned supports to design the shear walls?
The picture shows 4 approaches of modeling. In all cases, I showed the value of the deflection of same point (approximately the same point) at the top left corner of the bldg, and the value of the forces at the lower shear wall at right. The same load combination is used in all the models:
1.35 Dead + 1.05 Live - 1.5 Wind.
Model 1: Pinned supports
Model 2: Piles as linear spring (in x,y and z directions)
Model 3: Same as Model 2, but piles, in addition to the linear springs, are pinned in the bottom
Model 4: Piles as point springs.
I would much appreciate your help.
Please consider opening the link below to view a high resolution image. I don't know why Eng-Tips has very low resolution for the uploaded image (or do I miss something when using the upload feature?)
The link to the hi rest image:
I know the majority model their superstructure with supports as pinned/fixed even if there are piles beneath, but I figured out that maybe by modeling the piles I can simplify further tasks like pile design and mat foundation. The problem is that I have now very large deflections and very large moments on the shear walls. I don't know what to do with these forces. Should I revert to the model with pinned supports to design the shear walls?
The picture shows 4 approaches of modeling. In all cases, I showed the value of the deflection of same point (approximately the same point) at the top left corner of the bldg, and the value of the forces at the lower shear wall at right. The same load combination is used in all the models:
1.35 Dead + 1.05 Live - 1.5 Wind.
Model 1: Pinned supports
Model 2: Piles as linear spring (in x,y and z directions)
Model 3: Same as Model 2, but piles, in addition to the linear springs, are pinned in the bottom
Model 4: Piles as point springs.
I would much appreciate your help.
Please consider opening the link below to view a high resolution image. I don't know why Eng-Tips has very low resolution for the uploaded image (or do I miss something when using the upload feature?)
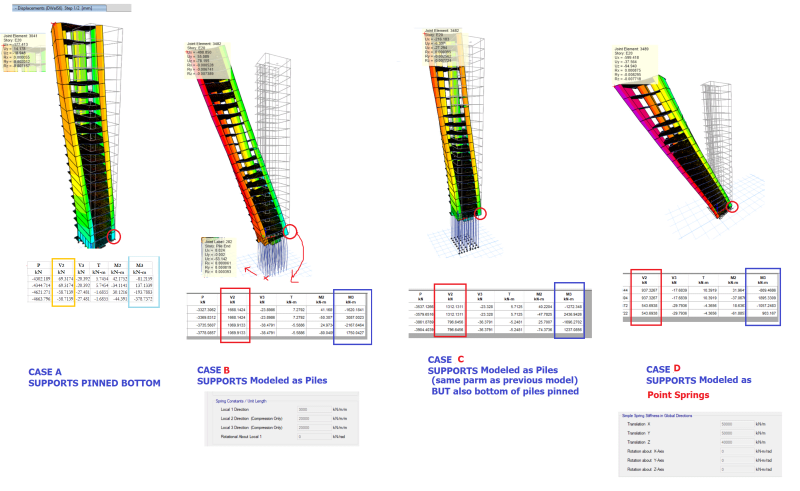
The link to the hi rest image: