Hello friends,
can you help me reduce the die cost of the part (3mm alloy steel):
the die workshop gave me a quotation of a four stages die:
1- forming the (plate like shape).
2- cutting center radius.
3- cutting half of the (small size cuts) on edge.
4-cutting other half (the rest of them).
he advises to separate the last stage into two stage to avoid work piece collapse due to fatigue.
and also he told me to prepare a pre-cut square sheets in order to eliminate a preparing cutting stage.
the annual production plan for this die is around 1000 per month, so, the die economics will fail the product.
i'm thinking of making the production plan as follows:
1-one forming stage.
2- laser cutting or the inner and outer small size cuts.
is this doable? one of my friends told me that i need to make it in a variable (z) laser cutting machine or a CNC punch machine.
kindly your advice will be most valuable.
Thank you.
can you help me reduce the die cost of the part (3mm alloy steel):
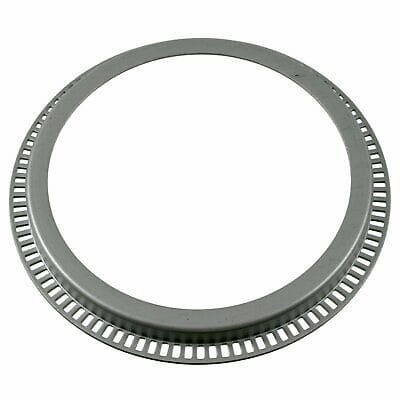
the die workshop gave me a quotation of a four stages die:
1- forming the (plate like shape).
2- cutting center radius.
3- cutting half of the (small size cuts) on edge.
4-cutting other half (the rest of them).
he advises to separate the last stage into two stage to avoid work piece collapse due to fatigue.
and also he told me to prepare a pre-cut square sheets in order to eliminate a preparing cutting stage.
the annual production plan for this die is around 1000 per month, so, the die economics will fail the product.
i'm thinking of making the production plan as follows:
1-one forming stage.
2- laser cutting or the inner and outer small size cuts.
is this doable? one of my friends told me that i need to make it in a variable (z) laser cutting machine or a CNC punch machine.
kindly your advice will be most valuable.
Thank you.