2bu3bdullah
Electrical
Hi,
Application is: Crude Oil Separation
VFD: Rockwell PowerFlex 753 (480V 60Hz Input, 52A/40HP 460V Output)
Motor: ABB 3-Phase Squirrel Cage Motor (480V Delta, 30kW, 60Hz, 1788 r/min, Class F, Duty S1)
Load: Centrifugal Separator connected to the motor through gearbox (1800 rpm to 4800rpm)
Using "Sensorless Vector Control" mode (Induction SV), we have success starting the motor from standstill or Fly starting from any speed (Even at low speeds).
The problem occurs during the cleaning of the Separator when discharging using high pressure water, this is acting as a shock load to the motor and the VFD is limiting the current by decreasing the output frequency which causes at least about 45 rpm speed reduction (We tested using water but if crude oil is used speed is expected to decrease > 150rpm).
The current limit is set to 78A which is the rated VFD overload current (78A for 3 Seconds), if the current limit is reduced the speed reduction will be more (~ 500 rpm) which is not accepted.
We are afraid that the VFD may trip if the shock loading is increased (current will exceed 78A for more than 3 seconds)
Any ideas how to enhance the performance of the VFD during the shock loading ?
Application is: Crude Oil Separation
VFD: Rockwell PowerFlex 753 (480V 60Hz Input, 52A/40HP 460V Output)
Motor: ABB 3-Phase Squirrel Cage Motor (480V Delta, 30kW, 60Hz, 1788 r/min, Class F, Duty S1)
Load: Centrifugal Separator connected to the motor through gearbox (1800 rpm to 4800rpm)
Using "Sensorless Vector Control" mode (Induction SV), we have success starting the motor from standstill or Fly starting from any speed (Even at low speeds).
The problem occurs during the cleaning of the Separator when discharging using high pressure water, this is acting as a shock load to the motor and the VFD is limiting the current by decreasing the output frequency which causes at least about 45 rpm speed reduction (We tested using water but if crude oil is used speed is expected to decrease > 150rpm).
The current limit is set to 78A which is the rated VFD overload current (78A for 3 Seconds), if the current limit is reduced the speed reduction will be more (~ 500 rpm) which is not accepted.
We are afraid that the VFD may trip if the shock loading is increased (current will exceed 78A for more than 3 seconds)
Any ideas how to enhance the performance of the VFD during the shock loading ?
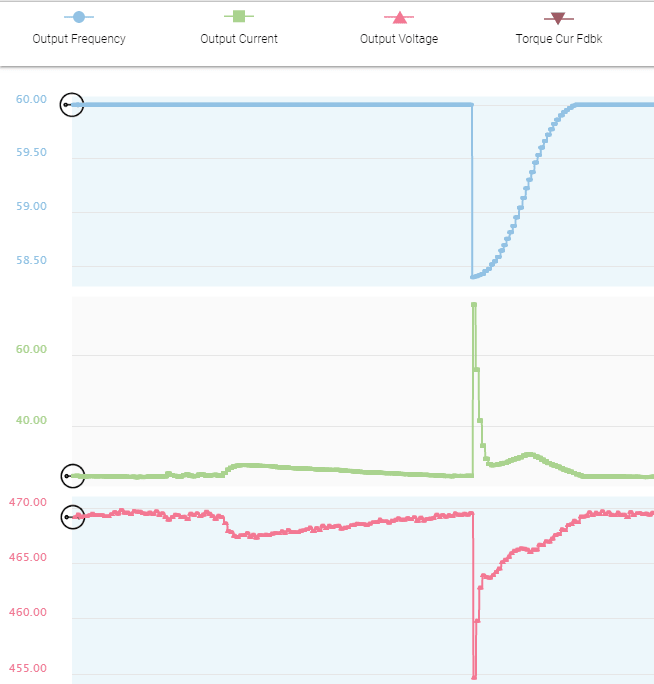