sendithard
Industrial
As I was a newbie learning gd&t the selection of the primary datum always seemed strange to me and I'm surprised it took me this long to ask this question.
If you drill from the top down thru a square part is it proper to keep the top surface as datum A or should you use the bottom for Datum A? I was taught manual inspection prior to learning GDT so my baseline goto is throw her down on the surface plate and that is your datum A...but that would be where the hole extrudes out of and not the entry location. Then I start thinking about the datum A of the threaded hole joining part only going halfway thru the part, so Datum A on top where the hole is tapped would be preferred, but can you somehow us the bottom of a blind hole part as datum A? I'm all confused on if there is proper use of the bottom and top surface as datum A.
This all hit me when learning projected tolerance zone. B/C do you project from said datum or is it perhaps implied the projection extends where parts meet, etc.
Attached is the pic that set my mind wondering dealing with projection tol zone. For instance, in the bottom pic I don't think it makes sense to use the bottom surface as datum A b/c it is a blind hole....but I have seen thru holes use both surfaces. So it makes me wonder could you use the bottom surface in the bottom pic as Datum A. And if so is that perhaps bad form. And then where would the projected tolerance start? Thanks as always.
If you drill from the top down thru a square part is it proper to keep the top surface as datum A or should you use the bottom for Datum A? I was taught manual inspection prior to learning GDT so my baseline goto is throw her down on the surface plate and that is your datum A...but that would be where the hole extrudes out of and not the entry location. Then I start thinking about the datum A of the threaded hole joining part only going halfway thru the part, so Datum A on top where the hole is tapped would be preferred, but can you somehow us the bottom of a blind hole part as datum A? I'm all confused on if there is proper use of the bottom and top surface as datum A.
This all hit me when learning projected tolerance zone. B/C do you project from said datum or is it perhaps implied the projection extends where parts meet, etc.
Attached is the pic that set my mind wondering dealing with projection tol zone. For instance, in the bottom pic I don't think it makes sense to use the bottom surface as datum A b/c it is a blind hole....but I have seen thru holes use both surfaces. So it makes me wonder could you use the bottom surface in the bottom pic as Datum A. And if so is that perhaps bad form. And then where would the projected tolerance start? Thanks as always.
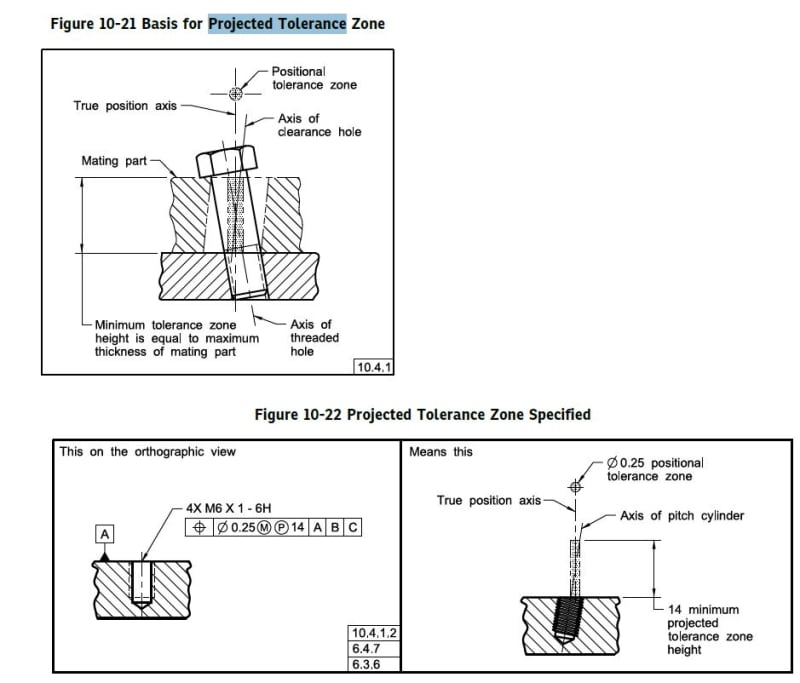