Redcobra2401
Automotive
thread71-400431 to further dive into alternative diesel engine designs, and I am by no means schooled in any areas regarding this just a general curiosity and Gained knowledge over the years.
The sleeve valve, side valve and one other "valve" type that is a rod with holes cut it that spins like a cam shaft has been tried.
But how about this. an rod under spring pressure in a cylinder, parallel with the cylinder bore, that protrudes into the head. Corresponding Slots cut into the side of the cylinder and rod to allow for the flow of air and exhaust. See illustration
It would reduce the amount of waisted space minamizing the loss of pressure during the combustion stroke and still allowing for high compression required for deisels. simplify manufacturing with the possibility of no need for a "head" to the cylinders making it able to be casted as a single peice to be bolted to a crank case.
What ya think? Any potential worth diving deeper into? And pardon the art skills it was just the get the idea jotted down before it disapeared. And high I'm new here.
The sleeve valve, side valve and one other "valve" type that is a rod with holes cut it that spins like a cam shaft has been tried.
But how about this. an rod under spring pressure in a cylinder, parallel with the cylinder bore, that protrudes into the head. Corresponding Slots cut into the side of the cylinder and rod to allow for the flow of air and exhaust. See illustration
It would reduce the amount of waisted space minamizing the loss of pressure during the combustion stroke and still allowing for high compression required for deisels. simplify manufacturing with the possibility of no need for a "head" to the cylinders making it able to be casted as a single peice to be bolted to a crank case.
What ya think? Any potential worth diving deeper into? And pardon the art skills it was just the get the idea jotted down before it disapeared. And high I'm new here.
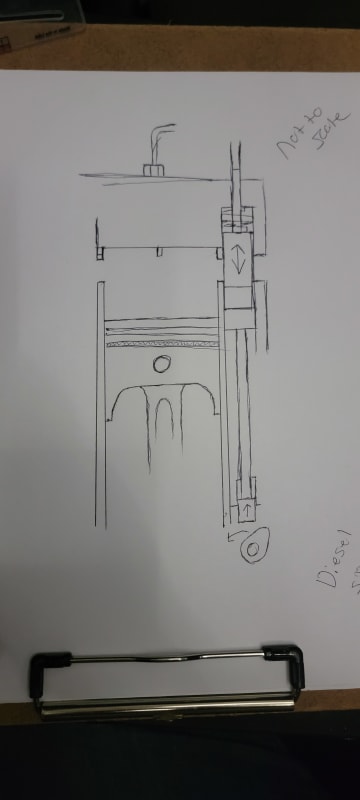