brewersean
Bioengineer
- Jul 21, 2022
- 8
Hi,
I have a very basic knowledge of electricity and motors, but have run into a bit of a bind.
I have a single phase 16A 22OV power supply for a 3 phase motor ( I am trying to install a VFD on.
I have two problems, the pump direction is backward (regardless of switching any of the WVU wires) and after about 42hz the VFD trips on ''Short Circuit/Current overload/Power Module protection''
I am lacking the understanding of what is actually happening when converting single to 3 phase, whether the capacitor is necessary or in the way, etc.
Can anyone shed any light on this?
Thanks!
Sean
I have a very basic knowledge of electricity and motors, but have run into a bit of a bind.
I have a single phase 16A 22OV power supply for a 3 phase motor ( I am trying to install a VFD on.
I have two problems, the pump direction is backward (regardless of switching any of the WVU wires) and after about 42hz the VFD trips on ''Short Circuit/Current overload/Power Module protection''
I am lacking the understanding of what is actually happening when converting single to 3 phase, whether the capacitor is necessary or in the way, etc.
Can anyone shed any light on this?
Thanks!
Sean
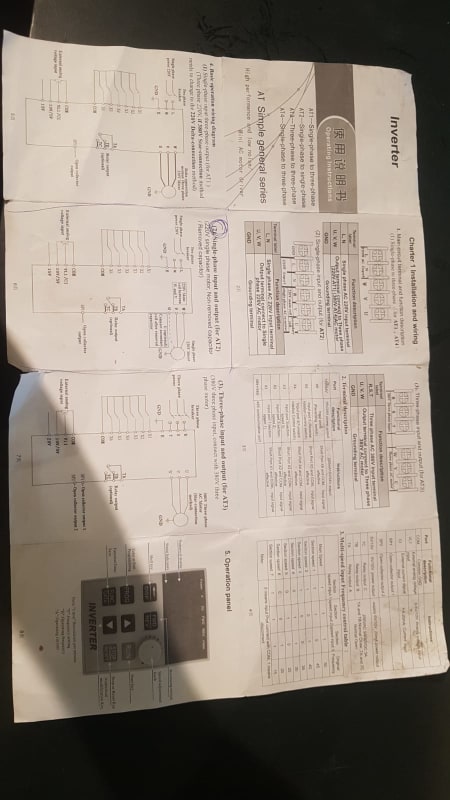