In ANSYS, I have been asked to take a 3D pressure vessel model and midsurface it to a shell model for FEA. See the section view in the image below. My red outline shows a change in thickness. Does anyone know of a clever way to handle this when simplifying to shells?
(before anyone asks, no an axisymmetric model is not suitable for this situation)
(before anyone asks, no an axisymmetric model is not suitable for this situation)
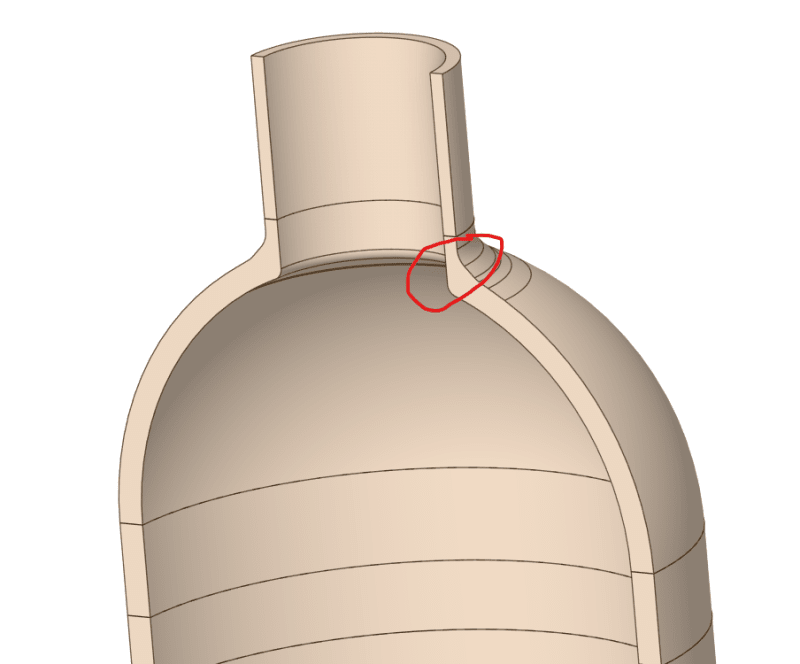