Darryll83
Mechanical
- Oct 1, 2008
- 4
I am working on modeling an assembly where a shaft is held with a bolted split clamp.
I not sure what is the best way to simplify this connection in the FE model.
I currently have the parts set as bonded together, but I feel like that's not quite right. I am thinking instead of putting a really stiff CBUSH between the shaft (pink) and the clamp (grey), and then replacing the bolts across the split with equivalent springs.
But I am curious if anyone else has a better idea.
Also, I am using MSC Apex / Nastran for the modeling.
I not sure what is the best way to simplify this connection in the FE model.
I currently have the parts set as bonded together, but I feel like that's not quite right. I am thinking instead of putting a really stiff CBUSH between the shaft (pink) and the clamp (grey), and then replacing the bolts across the split with equivalent springs.
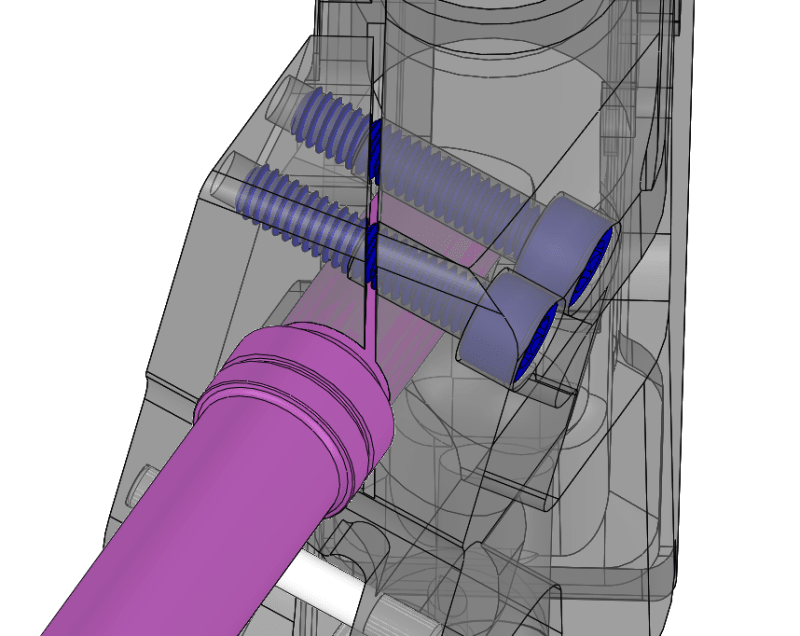
But I am curious if anyone else has a better idea.
Also, I am using MSC Apex / Nastran for the modeling.